SMT( মুদ্রিত সার্কিট বোর্ড সমাবেশ , পিসিবিএ ) এটিকে পৃষ্ঠ মাউন্ট প্রযুক্তিও বলা হয়।উত্পাদন প্রক্রিয়া চলাকালীন, সোল্ডার পেস্টটি উত্তপ্ত এবং গরম করার পরিবেশে গলে যায়, যাতে পিসিবি প্যাডগুলি সোল্ডার পেস্ট অ্যালয়ের মাধ্যমে পৃষ্ঠ মাউন্ট উপাদানগুলির সাথে নির্ভরযোগ্যভাবে একত্রিত হয়।আমরা এই প্রক্রিয়াটিকে রিফ্লো সোল্ডারিং বলি।রিফ্লো (রিফ্লো সোল্ডারিং) চলাকালীন বেশিরভাগ সার্কিট বোর্ড বোর্ড বাঁকানো এবং ওয়ার্পিং প্রবণ।গুরুতর ক্ষেত্রে, এটি এমনকি খালি সোল্ডারিং এবং সমাধির পাথরের মতো উপাদানগুলির কারণ হতে পারে। স্বয়ংক্রিয় সমাবেশ লাইনে, যদি সার্কিট বোর্ড কারখানার PCB সমতল না হয়, তাহলে এটি ভুল অবস্থানের কারণ হবে, বোর্ডের গর্ত এবং পৃষ্ঠ মাউন্ট প্যাডগুলিতে উপাদানগুলি ঢোকানো যাবে না এবং এমনকি স্বয়ংক্রিয় সন্নিবেশ মেশিনও ক্ষতিগ্রস্ত হবে।উপাদান সহ বোর্ড ঢালাই পরে বাঁকানো হয়, এবং উপাদান ফুট সুন্দরভাবে কাটা কঠিন।মেশিনের ভিতরে চ্যাসিস বা সকেটে বোর্ড ইনস্টল করা যায় না, তাই বোর্ড ওয়ারপিংয়ের সম্মুখীন হওয়া অ্যাসেম্বলি প্ল্যান্টের জন্যও খুব বিরক্তিকর।বর্তমানে, মুদ্রিত বোর্ডগুলি পৃষ্ঠের মাউন্টিং এবং চিপ মাউন্টিংয়ের যুগে প্রবেশ করেছে এবং সমাবেশ উদ্ভিদের অবশ্যই বোর্ড ওয়ার্পিংয়ের জন্য কঠোর এবং কঠোর প্রয়োজনীয়তা থাকতে হবে।
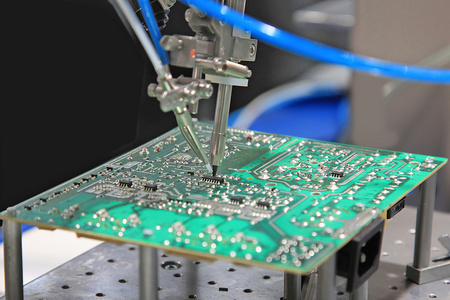
US IPC-6012 (1996 সংস্করণ) অনুসারে "এর জন্য স্পেসিফিকেশন এবং পারফরম্যান্স স্পেসিফিকেশন অনমনীয় মুদ্রিত বোর্ড ", পৃষ্ঠ-মাউন্ট করা মুদ্রিত বোর্ডগুলির জন্য সর্বাধিক অনুমোদিত ওয়ারপেজ এবং বিকৃতি হল 0.75%, এবং অন্যান্য বোর্ডগুলির জন্য 1.5%৷ IPC-RB-276 (1992 সংস্করণ) এর সাথে তুলনা করে, এটি সারফেস-মাউন্টেড প্রিন্টেড বোর্ডগুলির প্রয়োজনীয়তাকে উন্নত করেছে৷ বর্তমান, বিভিন্ন ইলেকট্রনিক সমাবেশ উদ্ভিদ দ্বারা অনুমোদিত যুদ্ধ পাতা, দ্বি-পার্শ্বযুক্ত বা বহু-স্তর নির্বিশেষে, 1.6 মিমি পুরুত্ব, সাধারণত 0.70~ 0.75% হয়।
অনেক SMT এবং BGA বোর্ডের জন্য, প্রয়োজন 0.5%।কিছু ইলেকট্রনিক কারখানা ওয়ারপেজের মান 0.3% বাড়ানোর জন্য তাগিদ দিচ্ছে।ওয়ারপেজ পরীক্ষা করার পদ্ধতি GB4677.5-84 বা IPC-TM-650.2.4.22B অনুযায়ী।প্রিন্ট করা বোর্ডটিকে যাচাইকৃত প্ল্যাটফর্মে রাখুন, টেস্ট পিনটি সেই জায়গায় ঢোকান যেখানে ওয়ারপেজের মাত্রা সবচেয়ে বেশি এবং টেস্ট পিনের ব্যাসকে মুদ্রিত বোর্ডের বাঁকা প্রান্তের দৈর্ঘ্য দিয়ে ভাগ করুন মুদ্রিত বোর্ড।বক্রতা চলে গেছে।

তাই পিসিবি তৈরির প্রক্রিয়ায়, বোর্ডের বাঁকানো এবং বক্র হওয়ার কারণ কী?
প্রতিটি প্লেট বাঁকানো এবং প্লেট ওয়ার্পিংয়ের কারণ আলাদা হতে পারে, তবে এটি সবই প্লেটে প্রয়োগ করা চাপের জন্য দায়ী করা উচিত যা প্লেট উপাদান সহ্য করতে পারে এমন চাপের চেয়ে বেশি।যখন প্লেটটি অসম চাপের শিকার হয় বা যখন বোর্ডের প্রতিটি স্থানের চাপ প্রতিরোধ করার ক্ষমতা অসম হয়, তখন বোর্ড বাঁকানো এবং বোর্ড ওয়ারিং এর ফলাফল ঘটবে।নীচে প্লেট বাঁকানো এবং প্লেট ওয়ার্পিংয়ের চারটি প্রধান কারণের সংক্ষিপ্তসার দেওয়া হল।
1. সার্কিট বোর্ডের অসম তামার পৃষ্ঠের ক্ষেত্রফল বোর্ডের বাঁকানো এবং ওয়ারিংকে আরও খারাপ করবে
সাধারণত, গ্রাউন্ডিংয়ের উদ্দেশ্যে সার্কিট বোর্ডে তামার ফয়েলের একটি বড় এলাকা ডিজাইন করা হয়।কখনও কখনও তামার ফয়েলের একটি বড় এলাকাও ভিসিসি স্তরে ডিজাইন করা হয়।যখন এই বৃহৎ এলাকার তামার ফয়েলগুলি একই সার্কিট বোর্ডে সমানভাবে বিতরণ করা যায় না, তখন এটি অসম তাপ শোষণ এবং তাপ অপচয়ের সমস্যা সৃষ্টি করবে।অবশ্যই, সার্কিট বোর্ড তাপের সাথে প্রসারিত এবং সংকুচিত হবে।যদি সম্প্রসারণ এবং সংকোচন একই সময়ে সঞ্চালিত না হয় তবে এটি বিভিন্ন চাপ এবং বিকৃতির কারণ হবে।এই সময়ে, যদি বোর্ডের তাপমাত্রা Tg মানের উপরের সীমাতে পৌঁছে যায়, বোর্ডটি নরম হতে শুরু করবে, স্থায়ী বিকৃতি ঘটাবে।
2. সার্কিট বোর্ডের ওজন নিজেই বোর্ডকে ডেন্ট এবং বিকৃত করতে পারে
সাধারণত, রিফ্লো ফার্নেস সার্কিট বোর্ডকে রিফ্লো ফার্নেসে এগিয়ে নিয়ে যাওয়ার জন্য একটি চেইন ব্যবহার করে, অর্থাৎ পুরো বোর্ডকে সমর্থন করার জন্য বোর্ডের দুই পাশে ফুলক্রাম হিসেবে ব্যবহার করা হয়।যদি বোর্ডে ভারী অংশ থাকে, বা বোর্ডের আকার খুব বড় হয়, এটি বীজের পরিমাণের কারণে মাঝখানে একটি বিষণ্নতা দেখাবে, যার ফলে প্লেটটি বাঁকবে।
3. ভি-কাটের গভীরতা এবং সংযোগকারী স্ট্রিপ জিগস-এর বিকৃতিকে প্রভাবিত করবে
মূলত, ভি-কাট হল অপরাধী যা বোর্ডের কাঠামোকে ধ্বংস করে, কারণ ভি-কাট মূল বড় শীটে ভি-আকৃতির খাঁজ কাটায়, তাই ভি-কাট বিকৃতির ঝুঁকিতে থাকে।
4. সার্কিট বোর্ডের প্রতিটি স্তরের সংযোগ পয়েন্ট (ভিয়াস) বোর্ডের প্রসারণ এবং সংকোচনকে সীমিত করবে
আজকের সার্কিট বোর্ডগুলি বেশিরভাগই মাল্টি-লেয়ার বোর্ড, এবং স্তরগুলির মধ্যে রিভেট-সদৃশ সংযোগ বিন্দু (মাধ্যমে) থাকবে।সংযোগ বিন্দু গর্ত, অন্ধ গর্ত এবং সমাহিত গর্ত মাধ্যমে বিভক্ত করা হয়.যেখানে সংযোগ পয়েন্ট আছে সেখানে বোর্ড সীমাবদ্ধ থাকবে।প্রসারণ এবং সংকোচনের প্রভাব পরোক্ষভাবে প্লেট বাঁকানো এবং প্লেট ওয়ারপিং সৃষ্টি করবে।
সুতরাং কিভাবে আমরা উত্পাদন প্রক্রিয়া চলাকালীন বোর্ড ওয়ারপিংয়ের সমস্যাটি আরও ভালভাবে প্রতিরোধ করতে পারি? এখানে কয়েকটি কার্যকর পদ্ধতি রয়েছে যা আমি আশা করি আপনাকে সাহায্য করতে পারে।
1. বোর্ডের চাপে তাপমাত্রার প্রভাব হ্রাস করুন
যেহেতু "তাপমাত্রা" হল বোর্ডের চাপের প্রধান উৎস, যতক্ষণ না রিফ্লো ওভেনের তাপমাত্রা কম হয় বা রিফ্লো ওভেনে বোর্ডের গরম ও শীতল হওয়ার হার কম হয়, ততক্ষণ প্লেট বাঁকানো এবং ওয়ারপেজের ঘটনা অনেক বেশি হতে পারে। হ্রাসযাইহোক, অন্যান্য পার্শ্ব প্রতিক্রিয়া ঘটতে পারে, যেমন সোল্ডার শর্ট সার্কিট।
2. উচ্চ Tg শীট ব্যবহার করা
Tg হল কাচের রূপান্তর তাপমাত্রা, অর্থাৎ যে তাপমাত্রায় উপাদানটি কাচের অবস্থা থেকে রাবার অবস্থায় পরিবর্তিত হয়।উপাদানটির Tg মান যত কম হবে, রিফ্লো ওভেনে প্রবেশ করার পরে বোর্ডটি যত দ্রুত নরম হতে শুরু করবে, এবং নরম রাবার অবস্থায় পরিণত হতে যে সময় লাগবে তা আরও দীর্ঘ হবে, এবং বোর্ডের বিকৃতি অবশ্যই আরও গুরুতর হবে। .একটি উচ্চ Tg শীট ব্যবহার চাপ এবং বিকৃতি সহ্য করার ক্ষমতা বাড়াতে পারে, কিন্তু আপেক্ষিক উপাদানের দামও বেশি।

3. সার্কিট বোর্ডের পুরুত্ব বাড়ান অনেক ইলেকট্রনিক পণ্যের জন্য লাইটার এবং পাতলা করার উদ্দেশ্য অর্জনের জন্য, বোর্ডের পুরুত্ব 1.0 মিমি, 0.8 মিমি বা এমনকি 0.6 মিমি রেখে গেছে।এই ধরনের বেধ অবশ্যই বোর্ডটিকে রিফ্লো ফার্নেসের পরে বিকৃত হওয়া থেকে রক্ষা করবে, যা সত্যিই কঠিন।এটি সুপারিশ করা হয় যে যদি হালকাতা এবং পাতলাতার জন্য কোন প্রয়োজন না থাকে তবে বোর্ডের পুরুত্ব 1.6 মিমি হওয়া উচিত, যা বোর্ডের নমন এবং বিকৃতির ঝুঁকিকে ব্যাপকভাবে কমাতে পারে। 4. সার্কিট বোর্ডের আকার হ্রাস করুন এবং ধাঁধার সংখ্যা হ্রাস করুন যেহেতু রিফ্লো ফার্নেসের বেশিরভাগই সার্কিট বোর্ডকে এগিয়ে নিয়ে যাওয়ার জন্য চেইন ব্যবহার করে, সার্কিট বোর্ডের আকার যত বড় হবে তার নিজস্ব ওজন, ডেন্ট এবং রিফ্লো ফার্নেসের বিকৃতির কারণে হবে, তাই সার্কিট বোর্ডের লম্বা দিকটি রাখার চেষ্টা করুন। বোর্ডের প্রান্ত হিসাবে।রিফ্লো ফার্নেসের চেইনে, সার্কিট বোর্ডের ওজন দ্বারা সৃষ্ট বিষণ্নতা এবং বিকৃতি হ্রাস করা যেতে পারে।প্যানেলের সংখ্যা হ্রাসও এই কারণে।অর্থাৎ, চুল্লিটি অতিক্রম করার সময়, যতদূর সম্ভব চুল্লির দিকটি পাস করার জন্য সরু প্রান্তটি ব্যবহার করার চেষ্টা করুন।বিষণ্নতা বিকৃতি পরিমাণ. 5. ব্যবহৃত চুল্লি ট্রে ফিক্সচার যদি উপরের পদ্ধতিগুলি অর্জন করা কঠিন হয়, শেষটি হল বিকৃতির পরিমাণ কমাতে রিফ্লো ক্যারিয়ার/টেমপ্লেট ব্যবহার করা।রিফ্লো ক্যারিয়ার/টেমপ্লেট প্লেটের বাঁক কমাতে পারে কারণ আশা করা যায় তা তাপীয় প্রসারণ বা ঠান্ডা সংকোচন।ট্রে সার্কিট বোর্ডকে ধরে রাখতে পারে এবং সার্কিট বোর্ডের তাপমাত্রা Tg মানের থেকে কম না হওয়া পর্যন্ত অপেক্ষা করতে পারে এবং আবার শক্ত হতে শুরু করে এবং এটি আসল আকারও বজায় রাখতে পারে। যদি একক-স্তর প্যালেট সার্কিট বোর্ডের বিকৃতি কমাতে না পারে, তাহলে উপরের এবং নীচের প্যালেটগুলির সাথে সার্কিট বোর্ডকে আটকাতে একটি কভার যোগ করতে হবে।এটি রিফ্লো ফার্নেসের মাধ্যমে সার্কিট বোর্ডের বিকৃতির সমস্যাকে ব্যাপকভাবে কমাতে পারে।যাইহোক, এই ফার্নেস ট্রে বেশ ব্যয়বহুল, এবং ট্রে স্থাপন এবং পুনর্ব্যবহার করতে কায়িক শ্রমের প্রয়োজন হয়। 6. সাব-বোর্ড ব্যবহার করতে V-Cut এর পরিবর্তে রাউটার ব্যবহার করুন যেহেতু V-Cut সার্কিট বোর্ডগুলির মধ্যে বোর্ডের কাঠামোগত শক্তিকে ধ্বংস করবে, তাই V-Cut সাব-বোর্ড ব্যবহার না করার বা V-কাটের গভীরতা কমানোর চেষ্টা করুন।
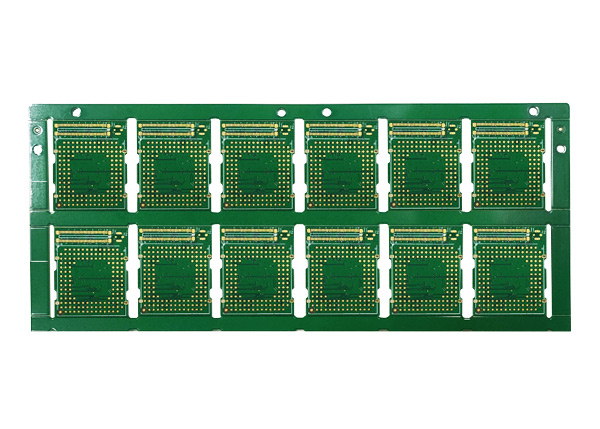
7. ইঞ্জিনিয়ারিং ডিজাইনে তিনটি পয়েন্ট চলে: উ: ইন্টারলেয়ার প্রিপ্রেগগুলির বিন্যাস প্রতিসম হওয়া উচিত, উদাহরণস্বরূপ, ছয়-স্তর বোর্ডের জন্য, 1~2 এবং 5~6 স্তরের মধ্যে পুরুত্ব এবং প্রিপ্রেগগুলির সংখ্যা একই হওয়া উচিত, অন্যথায় ল্যামিনেশনের পরে এটি মোটা করা সহজ। B. মাল্টি-লেয়ার কোর বোর্ড এবং প্রিপ্রেগ একই সরবরাহকারীর পণ্য ব্যবহার করা উচিত। C. বাইরের স্তরের A এবং পাশে B এর সার্কিট প্যাটার্নের ক্ষেত্রফল যতটা সম্ভব কাছাকাছি হওয়া উচিত।যদি A পাশটি একটি বড় তামার পৃষ্ঠ হয়, এবং B পাশে শুধুমাত্র কয়েকটি লাইন থাকে, তাহলে এই ধরনের মুদ্রিত বোর্ডটি এচিং করার পরে সহজেই বিকৃত হয়ে যাবে।যদি দুই পাশের লাইনের ক্ষেত্রফল খুব আলাদা হয়, তাহলে আপনি ভারসাম্যের জন্য পাতলা দিকে কিছু স্বাধীন গ্রিড যোগ করতে পারেন। 8. prepreg এর অক্ষাংশ এবং দ্রাঘিমাংশ: প্রিপ্রেগ স্তরিত হওয়ার পরে, ওয়ার্প এবং ওয়েফ্ট সংকোচনের হার আলাদা হয় এবং ব্ল্যাঙ্কিং এবং ল্যামিনেশনের সময় ওয়ার্প এবং ওয়েফটের দিকগুলিকে আলাদা করতে হবে।অন্যথায়, ল্যামিনেশনের পরে সমাপ্ত বোর্ডটি বিকৃত করা সহজ এবং বেকিং বোর্ডে চাপ প্রয়োগ করা হলেও এটি সংশোধন করা কঠিন।মাল্টিলেয়ার বোর্ডের ওয়ারপেজের অনেক কারণ হল ল্যামিনেশনের সময় প্রিপ্রেগগুলিকে ওয়ার্প এবং ওয়েফটের দিক থেকে আলাদা করা যায় না এবং সেগুলি এলোমেলোভাবে স্ট্যাক করা হয়। ওয়ার্প এবং ওয়েফটের দিকগুলিকে আলাদা করার পদ্ধতি: একটি রোলে প্রিপ্রেগের ঘূর্ণায়মান দিকটি হল ওয়ার্প দিক, যখন প্রস্থের দিকটি হল ওয়েফট দিক;কপার ফয়েল বোর্ডের জন্য, লম্বা দিকটি হল ওয়েফট দিক এবং ছোট দিকটি হল ওয়ার্প দিক।আপনি যদি নিশ্চিত না হন, অনুগ্রহ করে প্রস্তুতকারক বা সরবরাহকারীর সাথে যোগাযোগ করুন। 9. কাটার আগে বেকিং বোর্ড: তামা পরিহিত ল্যামিনেট (150 ডিগ্রি সেলসিয়াস, সময় 8±2 ঘন্টা) কাটার আগে বোর্ড বেক করার উদ্দেশ্য হল বোর্ডের আর্দ্রতা অপসারণ করা এবং একই সাথে বোর্ডের রজন সম্পূর্ণরূপে শক্ত করা এবং আরও দূর করা। বোর্ডে অবশিষ্ট স্ট্রেস, যা বোর্ডকে বিকৃত হওয়া থেকে রোধ করতে কার্যকর।সাহায্য করছে।বর্তমানে, অনেক দ্বি-পার্শ্বযুক্ত এবং বহু-স্তর বোর্ডগুলি এখনও খালি করার আগে বা পরে বেক করার ধাপকে মেনে চলে।তবে কিছু প্লেট কারখানার ক্ষেত্রে ব্যতিক্রম রয়েছে।বিভিন্ন PCB কারখানার বর্তমান PCB শুকানোর সময় বিধিগুলিও অসঙ্গত, 4 থেকে 10 ঘন্টা পর্যন্ত।উত্পাদিত মুদ্রিত বোর্ডের গ্রেড এবং ওয়ারপেজের জন্য গ্রাহকের প্রয়োজনীয়তা অনুসারে সিদ্ধান্ত নেওয়ার সুপারিশ করা হয়।পুরো ব্লক বেক হওয়ার পরে একটি জিগসতে কাটা বা ফাঁকা করার পরে বেক করুন।উভয় পদ্ধতিই সম্ভব।কাটার পরে বোর্ড বেক করার পরামর্শ দেওয়া হয়।ভিতরের স্তর বোর্ডটিও বেক করা উচিত ... 10. ল্যামিনেশনের পরে চাপ ছাড়াও: মাল্টি-লেয়ার বোর্ড গরম-চাপা এবং ঠান্ডা চাপার পরে, এটি বের করা হয়, কাটা বা মিশ্রিত করা হয় এবং তারপর 4 ঘন্টার জন্য 150 ডিগ্রি সেলসিয়াস তাপমাত্রায় একটি ওভেনে ফ্ল্যাট করে রাখা হয়, যাতে বোর্ডে চাপ থাকে। ধীরে ধীরে মুক্তি এবং রজন সম্পূর্ণরূপে নিরাময় করা হয়.এই পদক্ষেপ বাদ দেওয়া যাবে না.
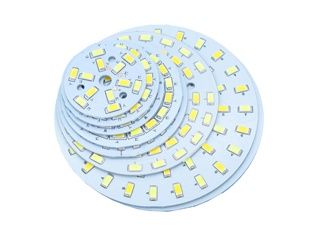
11. ইলেক্ট্রোপ্লেটিং এর সময় পাতলা প্লেটকে সোজা করতে হবে: যখন 0.4~0.6mm অতি-পাতলা মাল্টিলেয়ার বোর্ড পৃষ্ঠের ইলেক্ট্রোপ্লেটিং এবং প্যাটার্ন ইলেক্ট্রোপ্লেটিং এর জন্য ব্যবহার করা হয়, বিশেষ ক্ল্যাম্পিং রোলার তৈরি করা উচিত।স্বয়ংক্রিয় ইলেক্ট্রোপ্লেটিং লাইনে ফ্লাই বাসে পাতলা প্লেটটি আটকানোর পরে, পুরো ফ্লাই বাসটিকে আটকানোর জন্য একটি বৃত্তাকার লাঠি ব্যবহার করা হয়।রোলারগুলির সমস্ত প্লেট সোজা করার জন্য রোলারগুলিকে একত্রিত করা হয় যাতে প্রলেপ দেওয়ার পরে প্লেটগুলি বিকৃত না হয়।এই পরিমাপ ছাড়া, 20 থেকে 30 মাইক্রনের একটি তামার স্তর ইলেক্ট্রোপ্লেট করার পরে, শীটটি বাঁকবে এবং এটি প্রতিকার করা কঠিন। 12. গরম বাতাস সমতল করার পরে বোর্ডের শীতলকরণ: যখন প্রিন্ট করা বোর্ড গরম বাতাস দ্বারা সমতল করা হয়, তখন এটি সোল্ডার বাথের উচ্চ তাপমাত্রা (প্রায় 250 ডিগ্রি সেলসিয়াস) দ্বারা প্রভাবিত হয়।বের করে নেওয়ার পরে, এটি প্রাকৃতিক শীতল করার জন্য একটি সমতল মার্বেল বা ইস্পাত প্লেটে স্থাপন করা উচিত এবং তারপরে পরিষ্কারের জন্য একটি পোস্ট-প্রসেসিং মেশিনে পাঠানো উচিত।এটি বোর্ডের ওয়ারপেজ প্রতিরোধের জন্য ভাল।কিছু কারখানায়, সীসা-টিনের পৃষ্ঠের উজ্জ্বলতা বাড়ানোর জন্য, গরম বাতাস সমতল হওয়ার পরপরই বোর্ডগুলিকে ঠান্ডা জলে রাখা হয় এবং তারপর কয়েক সেকেন্ড পরে পোস্ট-প্রসেসিংয়ের জন্য বের করা হয়।এই ধরনের গরম এবং ঠান্ডা প্রভাব নির্দিষ্ট ধরনের বোর্ডে ওয়ারিং হতে পারে।পাকানো, স্তরযুক্ত বা ফোস্কাযুক্ত।এছাড়াও, শীতল করার জন্য সরঞ্জামগুলিতে একটি এয়ার ফ্লোটেশন বিছানা ইনস্টল করা যেতে পারে। 13. বিকৃত বোর্ডের চিকিত্সা: একটি সু-পরিচালিত কারখানায়, চূড়ান্ত পরিদর্শনের সময় মুদ্রিত বোর্ডটি 100% সমতলতা পরীক্ষা করা হবে।সমস্ত অযোগ্য বোর্ডগুলিকে বাছাই করা হবে, ওভেনে রাখা হবে, 150 ডিগ্রি সেলসিয়াসে 3-6 ঘন্টার জন্য ভারী চাপে বেক করা হবে এবং ভারী চাপে প্রাকৃতিকভাবে ঠান্ডা করা হবে।তারপরে বোর্ডটি বের করার চাপ থেকে উপশম করুন, এবং সমতলতা পরীক্ষা করুন, যাতে বোর্ডের অংশটি সংরক্ষণ করা যায় এবং কিছু বোর্ড বেক করতে হবে এবং তাদের সমতল করার আগে দুই বা তিনবার চাপ দিতে হবে।যদি উপরে উল্লিখিত অ্যান্টি-ওয়ার্পিং প্রক্রিয়া ব্যবস্থাগুলি বাস্তবায়িত না হয়, তবে কিছু বোর্ড অকেজো হয়ে যাবে এবং শুধুমাত্র বাতিল করা যেতে পারে।