SMT( அச்சிடப்பட்ட சர்க்யூட் போர்டு சட்டசபை , பிசிபிஏ ) மேற்பரப்பு ஏற்ற தொழில்நுட்பம் என்றும் அழைக்கப்படுகிறது.உற்பத்திச் செயல்பாட்டின் போது, சாலிடர் பேஸ்ட் சூடுபடுத்தப்பட்டு சூடாக்கும் சூழலில் உருகுகிறது, இதனால் பிசிபி பேட்கள் சாலிடர் பேஸ்ட் அலாய் மூலம் மேற்பரப்பு ஏற்ற கூறுகளுடன் நம்பகத்தன்மையுடன் இணைக்கப்படுகின்றன.இந்த செயல்முறையை reflow சாலிடரிங் என்று அழைக்கிறோம்.பெரும்பாலான சர்க்யூட் போர்டுகள் ரீஃப்ளோ (ரிஃப்ளோ சாலிடரிங்) செய்யும்போது பலகை வளைந்து வளைந்து போக வாய்ப்புள்ளது.கடுமையான சந்தர்ப்பங்களில், இது வெற்று சாலிடரிங் மற்றும் கல்லறைக் கற்கள் போன்ற கூறுகளை ஏற்படுத்தக்கூடும். தானியங்கு அசெம்பிளி லைனில், சர்க்யூட் போர்டு தொழிற்சாலையின் PCB தட்டையாக இல்லாவிட்டால், அது துல்லியமற்ற நிலைப்பாட்டை ஏற்படுத்தும், போர்டின் துளைகள் மற்றும் மேற்பரப்பு மவுண்ட் பேட்களில் கூறுகளை செருக முடியாது, மேலும் தானியங்கி செருகும் இயந்திரம் கூட சேதமடையும்.கூறுகளுடன் கூடிய பலகை வெல்டிங்கிற்குப் பிறகு வளைந்திருக்கும், மற்றும் கூறு கால்களை நேர்த்தியாக வெட்டுவது கடினம்.இயந்திரத்தின் உள்ளே சேஸ் அல்லது சாக்கெட்டில் பலகையை நிறுவ முடியாது, எனவே போர்டு வார்ப்பிங்கை சந்திப்பது சட்டசபை ஆலைக்கு மிகவும் எரிச்சலூட்டும்.தற்போது, அச்சிடப்பட்ட பலகைகள் மேற்பரப்பு மவுண்டிங் மற்றும் சிப் மவுண்டிங் சகாப்தத்தில் நுழைந்துள்ளன, மேலும் அசெம்பிளி ஆலைகள் போர்டு வார்ப்பிங்கிற்கான கடுமையான மற்றும் கடுமையான தேவைகளைக் கொண்டிருக்க வேண்டும்.
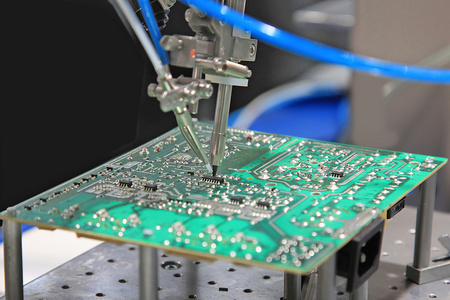
US IPC-6012 (1996 பதிப்பு) படி "குறிப்பிடுதல் மற்றும் செயல்திறன் விவரக்குறிப்பு கடுமையான அச்சிடப்பட்ட பலகைகள் ", மேற்பரப்பில் பொருத்தப்பட்ட அச்சிடப்பட்ட பலகைகளுக்கான அதிகபட்ச அனுமதிக்கக்கூடிய வார்பேஜ் மற்றும் சிதைவு 0.75% மற்றும் பிற பலகைகளுக்கு 1.5% ஆகும். IPC-RB-276 (1992 பதிப்பு) உடன் ஒப்பிடும்போது, இது மேற்பரப்பில் பொருத்தப்பட்ட அச்சிடப்பட்ட பலகைகளுக்கான தேவைகளை மேம்படுத்தியுள்ளது. தற்போது, பல்வேறு எலக்ட்ரானிக் அசெம்பிளி ஆலைகளால் அனுமதிக்கப்படும் வார்பேஜ், இரட்டை பக்க அல்லது பல அடுக்கு, 1.6 மிமீ தடிமன், பொதுவாக 0.70~0.75% ஆகும்.
பல SMT மற்றும் BGA போர்டுகளுக்கு, 0.5% தேவை.சில மின்னணு தொழிற்சாலைகள் வார்பேஜ் தரத்தை 0.3% ஆக உயர்த்த வலியுறுத்துகின்றன.வார்பேஜ் சோதனை முறை GB4677.5-84 அல்லது IPC-TM-650.2.4.22B இன் படி உள்ளது.சரிபார்க்கப்பட்ட மேடையில் அச்சிடப்பட்ட பலகையை வைத்து, வார்பேஜ் அளவு அதிகமாக இருக்கும் இடத்தில் சோதனைப் பின்னைச் செருகவும், சோதனை முள் விட்டத்தை அச்சிடப்பட்ட பலகையின் வளைந்த விளிம்பின் நீளத்தால் வகுக்கவும். அச்சிடப்பட்ட பலகை.வளைவு போய்விட்டது.

எனவே PCB உற்பத்தி செயல்பாட்டில், பலகையின் வளைவு மற்றும் சிதைவுக்கான காரணங்கள் என்ன?
ஒவ்வொரு தட்டு வளைவதற்கும் தட்டு சிதைவதற்கும் காரணம் வேறுபட்டிருக்கலாம், ஆனால் தட்டுப் பொருள் தாங்கக்கூடிய அழுத்தத்தை விட அதிகமாக இருக்கும் தட்டுக்கு ஏற்படும் அழுத்தமே இவை அனைத்தும் காரணமாக இருக்க வேண்டும்.தட்டு சீரற்ற அழுத்தத்திற்கு ஆளாகும் போது அல்லது பலகையில் உள்ள ஒவ்வொரு இடமும் அழுத்தத்தை எதிர்க்கும் திறன் சீரற்றதாக இருக்கும் போது, பலகை வளைந்து பலகை வார்ப்பிங் விளைவாக ஏற்படும்.பின்வரும் நான்கு முக்கிய காரணங்களின் சுருக்கம் தட்டு வளைவு மற்றும் தட்டு சிதைவு.
1. சர்க்யூட் போர்டில் உள்ள சீரற்ற செப்புப் பரப்பு பலகையின் வளைவு மற்றும் சிதைவை மோசமாக்கும்
பொதுவாக, செப்புப் படலத்தின் ஒரு பெரிய பகுதியானது சர்க்யூட் போர்டில் தரையிறக்கும் நோக்கங்களுக்காக வடிவமைக்கப்பட்டுள்ளது.சில சமயங்களில் செப்புப் படலத்தின் ஒரு பெரிய பகுதி Vcc லேயரில் வடிவமைக்கப்பட்டுள்ளது.இந்த பெரிய பரப்பளவு கொண்ட செப்புத் தகடுகளை ஒரே சர்க்யூட் போர்டில் சமமாக விநியோகிக்க முடியாதபோது, அது சீரற்ற வெப்ப உறிஞ்சுதல் மற்றும் வெப்பச் சிதறல் போன்ற பிரச்சனைகளை ஏற்படுத்தும்.நிச்சயமாக, சர்க்யூட் போர்டு வெப்பத்துடன் விரிவடைந்து சுருங்கும்.விரிவாக்கம் மற்றும் சுருக்கத்தை ஒரே நேரத்தில் செய்ய முடியாவிட்டால், அது வெவ்வேறு மன அழுத்தம் மற்றும் சிதைவை ஏற்படுத்தும்.இந்த நேரத்தில், பலகையின் வெப்பநிலை Tg மதிப்பின் மேல் வரம்பை அடைந்தால், பலகை மென்மையாக்கத் தொடங்கும், இது நிரந்தர சிதைவை ஏற்படுத்தும்.
2. சர்க்யூட் போர்டின் எடையே பலகையில் பள்ளம் மற்றும் சிதைவை ஏற்படுத்தும்
பொதுவாக, ரிஃப்ளோ ஃபர்னேஸ், ரிஃப்ளோ ஃபர்னேஸில் சர்க்யூட் போர்டை முன்னோக்கி இயக்க ஒரு சங்கிலியைப் பயன்படுத்துகிறது, அதாவது பலகையின் இரு பக்கங்களும் முழு பலகையையும் ஆதரிக்க ஃபுல்க்ரம்களாகப் பயன்படுத்தப்படுகின்றன.பலகையில் கனமான பாகங்கள் இருந்தாலோ, அல்லது பலகையின் அளவு பெரிதாக இருந்தாலோ, விதையின் அளவு காரணமாக நடுவில் ஒரு மந்தநிலையைக் காட்டும், இதனால் தட்டு வளைந்துவிடும்.
3. வி-கட் மற்றும் இணைக்கும் பட்டையின் ஆழம் ஜிக்சாவின் சிதைவை பாதிக்கும்
அடிப்படையில், V-கட் என்பது பலகையின் கட்டமைப்பை அழிக்கும் குற்றவாளி, ஏனெனில் V-கட் அசல் பெரிய தாளில் V- வடிவ பள்ளங்களை வெட்டுகிறது, எனவே V-கட் சிதைவதற்கு வாய்ப்புள்ளது.
4. சர்க்யூட் போர்டில் உள்ள ஒவ்வொரு அடுக்கின் இணைப்புப் புள்ளிகள் (வழிகள்) பலகையின் விரிவாக்கம் மற்றும் சுருக்கத்தை கட்டுப்படுத்தும்
இன்றைய சர்க்யூட் போர்டுகளில் பெரும்பாலும் பல அடுக்கு பலகைகள் உள்ளன, மேலும் அடுக்குகளுக்கு இடையில் ரிவெட் போன்ற இணைப்புப் புள்ளிகள் (வழியாக) இருக்கும்.இணைப்பு புள்ளிகள் துளைகள், குருட்டு துளைகள் மற்றும் புதைக்கப்பட்ட துளைகள் மூலம் பிரிக்கப்படுகின்றன.இணைப்பு புள்ளிகள் இருக்கும் இடங்களில், பலகை கட்டுப்படுத்தப்படும்.விரிவாக்கம் மற்றும் சுருங்குதலின் விளைவும் மறைமுகமாக தட்டு வளைவு மற்றும் தட்டு சிதைவை ஏற்படுத்தும்.
உற்பத்திச் செயல்பாட்டின் போது பலகை வார்ப்பிங் சிக்கலை எவ்வாறு சிறப்பாகத் தடுக்கலாம்? உங்களுக்கு உதவக்கூடிய சில பயனுள்ள முறைகள் இங்கே உள்ளன.
1. பலகையின் அழுத்தத்தில் வெப்பநிலையின் விளைவைக் குறைக்கவும்
"வெப்பநிலை" என்பது பலகை அழுத்தத்தின் முக்கிய ஆதாரமாக இருப்பதால், ரிஃப்ளோ அடுப்பின் வெப்பநிலை குறைக்கப்படும் வரை அல்லது ரிஃப்ளோ அடுப்பில் பலகையை சூடாக்கும் மற்றும் குளிர்விக்கும் வேகம் குறையும் வரை, தட்டு வளைவு மற்றும் வார்பேஜ் ஆகியவை பெருமளவில் ஏற்படலாம். குறைக்கப்பட்டது.இருப்பினும், சாலிடர் ஷார்ட் சர்க்யூட் போன்ற பிற பக்க விளைவுகள் ஏற்படலாம்.
2. உயர் Tg தாளைப் பயன்படுத்துதல்
Tg என்பது கண்ணாடி மாற்ற வெப்பநிலை, அதாவது கண்ணாடி நிலையிலிருந்து ரப்பர் நிலைக்கு பொருள் மாறும் வெப்பநிலை.பொருளின் Tg மதிப்பு குறைவாக இருந்தால், ரிஃப்ளோ அடுப்பில் நுழைந்தவுடன் பலகை வேகமாக மென்மையாக மாறத் தொடங்குகிறது, மேலும் மென்மையான ரப்பர் நிலையாக மாற எடுக்கும் நேரம் அது நீண்டதாக மாறும், மேலும் பலகையின் சிதைவு நிச்சயமாக மிகவும் தீவிரமாக இருக்கும். .அதிக Tg தாளைப் பயன்படுத்துவது மன அழுத்தம் மற்றும் சிதைவைத் தாங்கும் திறனை அதிகரிக்கும், ஆனால் தொடர்புடைய பொருளின் விலையும் அதிகமாக உள்ளது.

3. சர்க்யூட் போர்டின் தடிமன் அதிகரிக்கவும் பல எலக்ட்ரானிக் தயாரிப்புகளுக்கு இலகுவான மற்றும் மெல்லிய நோக்கத்தை அடைவதற்காக, பலகையின் தடிமன் 1.0 மிமீ, 0.8 மிமீ அல்லது 0.6 மிமீ கூட விடப்பட்டுள்ளது.அத்தகைய தடிமன் ரீஃப்ளோ உலைக்குப் பிறகு பலகையை சிதைப்பதைத் தடுக்க வேண்டும், இது மிகவும் கடினம்.இலேசான தன்மை மற்றும் மெல்லிய தன்மைக்கான தேவை இல்லை என்றால், பலகையின் தடிமன் 1.6 மிமீ இருக்க வேண்டும் என்று பரிந்துரைக்கப்படுகிறது, இது பலகையின் வளைவு மற்றும் சிதைவின் அபாயத்தை வெகுவாகக் குறைக்கும். 4. சர்க்யூட் போர்டின் அளவைக் குறைத்து, புதிர்களின் எண்ணிக்கையைக் குறைக்கவும் பெரும்பாலான ரிஃப்ளோ உலைகள் சர்க்யூட் போர்டை முன்னோக்கி இயக்க சங்கிலிகளைப் பயன்படுத்துவதால், சர்க்யூட் போர்டின் பெரிய அளவு அதன் சொந்த எடை, பள்ளம் மற்றும் ரிஃப்ளோ ஃபர்னேஸில் உள்ள சிதைவின் காரணமாக இருக்கும், எனவே சர்க்யூட் போர்டின் நீண்ட பக்கத்தை வைக்க முயற்சிக்கவும். பலகையின் விளிம்பாக.ரிஃப்ளோ உலைகளின் சங்கிலியில், சர்க்யூட் போர்டின் எடையால் ஏற்படும் மனச்சோர்வு மற்றும் சிதைவைக் குறைக்கலாம்.பேனல்களின் எண்ணிக்கை குறைப்பும் இந்த காரணத்தை அடிப்படையாகக் கொண்டது.அதாவது, உலையைக் கடக்கும்போது, குறுகிய விளிம்பைப் பயன்படுத்தி உலை திசையை முடிந்தவரை கடக்க முயற்சிக்கவும்.மனச்சோர்வு சிதைவின் அளவு. 5. பயன்படுத்திய உலை தட்டு பொருத்தம் மேலே உள்ள முறைகளை அடைவது கடினமாக இருந்தால், கடைசியாக ரிஃப்ளோ கேரியர்/டெம்ப்ளேட்டைப் பயன்படுத்தி சிதைவின் அளவைக் குறைக்க வேண்டும்.ரிஃப்ளோ கேரியர்/டெம்ப்ளேட் தட்டின் வளைவைக் குறைக்கக் காரணம், அது வெப்ப விரிவாக்கமா அல்லது குளிர்ச்சியான சுருக்கமா என நம்பப்படுகிறது.தட்டு சர்க்யூட் போர்டைப் பிடித்து, சர்க்யூட் போர்டின் வெப்பநிலை Tg மதிப்பை விடக் குறைவாக இருக்கும் வரை காத்திருந்து, மீண்டும் கடினமாக்கத் தொடங்கும், மேலும் அது அசல் அளவையும் பராமரிக்கலாம். ஒற்றை அடுக்கு பலகை சர்க்யூட் போர்டின் சிதைவைக் குறைக்க முடியாவிட்டால், சர்க்யூட் போர்டை மேல் மற்றும் கீழ் தட்டுகளுடன் இறுக்குவதற்கு ஒரு கவர் சேர்க்கப்பட வேண்டும்.இது ரிஃப்ளோ உலை மூலம் சர்க்யூட் போர்டு சிதைவின் சிக்கலை வெகுவாகக் குறைக்கும்.இருப்பினும், இந்த உலை தட்டு மிகவும் விலை உயர்ந்தது, மேலும் தட்டுகளை வைப்பதற்கும் மறுசுழற்சி செய்வதற்கும் உடல் உழைப்பு தேவைப்படுகிறது. 6. சப்-போர்டைப் பயன்படுத்த V-Cutக்குப் பதிலாக ரூட்டரைப் பயன்படுத்தவும் சர்க்யூட் போர்டுகளுக்கு இடையே உள்ள பலகையின் கட்டமைப்பு வலிமையை V-கட் அழித்துவிடும் என்பதால், V-Cut துணைப் பலகையைப் பயன்படுத்த வேண்டாம் அல்லது V-கட்டின் ஆழத்தைக் குறைக்க முயற்சிக்கவும்.
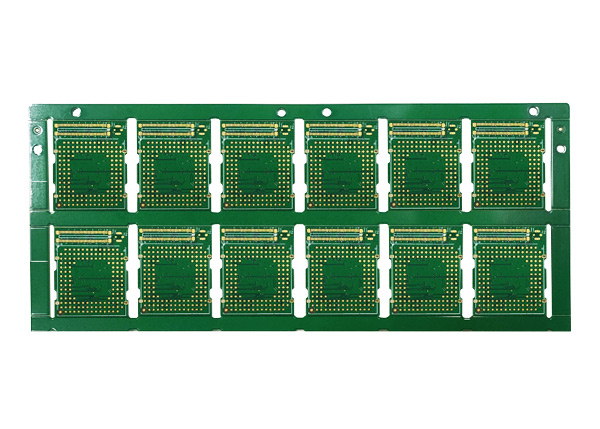
7. பொறியியல் வடிவமைப்பில் மூன்று புள்ளிகள் இயங்குகின்றன: A. இன்டர்லேயர் ப்ரீப்ரெக்ஸின் ஏற்பாடு சமச்சீராக இருக்க வேண்டும், எடுத்துக்காட்டாக, ஆறு அடுக்கு பலகைகளுக்கு, 1~2 மற்றும் 5~6 அடுக்குகளுக்கு இடையேயான தடிமன் மற்றும் ப்ரீப்ரெக்ஸின் எண்ணிக்கை ஒரே மாதிரியாக இருக்க வேண்டும், இல்லையெனில் லேமினேஷனுக்குப் பிறகு வார்ப் செய்வது எளிது. B. மல்டி-லேயர் கோர் போர்டு மற்றும் ப்ரீப்ரெக் ஆகியவை ஒரே சப்ளையர் தயாரிப்புகளைப் பயன்படுத்த வேண்டும். C. வெளிப்புற அடுக்கின் A மற்றும் பக்க B இல் உள்ள சுற்று வடிவத்தின் பரப்பளவு முடிந்தவரை நெருக்கமாக இருக்க வேண்டும்.A பக்கம் ஒரு பெரிய செப்பு மேற்பரப்பு மற்றும் B பக்கத்தில் ஒரு சில கோடுகள் இருந்தால், இந்த வகையான அச்சிடப்பட்ட பலகை பொறித்த பிறகு எளிதில் சிதைந்துவிடும்.இரண்டு பக்கங்களிலும் உள்ள கோடுகளின் பரப்பளவு மிகவும் வித்தியாசமாக இருந்தால், சமநிலைக்காக மெல்லிய பக்கத்தில் சில சுயாதீன கட்டங்களைச் சேர்க்கலாம். 8. அட்சரேகை மற்றும் தீர்க்கரேகை: ப்ரீப்ரெக் லேமினேட் செய்யப்பட்ட பிறகு, வார்ப் மற்றும் வெஃப்ட் சுருக்க விகிதங்கள் வேறுபட்டவை, மேலும் வெற்று மற்றும் லேமினேஷனின் போது வார்ப் மற்றும் வெஃப்ட் திசைகள் வேறுபடுத்தப்பட வேண்டும்.இல்லையெனில், லேமினேஷனுக்குப் பிறகு முடிக்கப்பட்ட பலகையை சிதைப்பது எளிது, மேலும் பேக்கிங் போர்டில் அழுத்தம் கொடுக்கப்பட்டாலும் அதை சரிசெய்வது கடினம்.மல்டிலேயர் போர்டின் போர்பேஜிற்கான பல காரணங்கள், லேமினேஷனின் போது வார்ப் மற்றும் வெஃப்ட் திசைகளில் ப்ரீப்ரெக்ஸ் வேறுபடுவதில்லை, மேலும் அவை சீரற்ற முறையில் அடுக்கி வைக்கப்படுகின்றன. வார்ப் மற்றும் வெஃப்ட் திசைகளை வேறுபடுத்துவதற்கான முறை: ஒரு ரோலில் ப்ரீப்ரெக்கின் உருளும் திசையானது வார்ப் திசையாகும், அதே சமயம் அகலத்தின் திசையானது வெஃப்ட் திசையாகும்;செப்புப் படலப் பலகைக்கு, நீண்ட பக்கம் வெஃப்ட் திசையாகவும், குறுகிய பக்கம் வார்ப் திசையாகவும் இருக்கும்.உங்களுக்குத் தெரியாவிட்டால், உற்பத்தியாளர் அல்லது சப்ளையர் வினவலைத் தொடர்பு கொள்ளவும். 9. வெட்டுவதற்கு முன் பேக்கிங் போர்டு: செப்பு உடையணிந்த லேமினேட்டை (150 டிகிரி செல்சியஸ், நேரம் 8±2 மணிநேரம்) வெட்டுவதற்கு முன் பலகையை சுடுவதன் நோக்கம் பலகையில் உள்ள ஈரப்பதத்தை நீக்குவதும், அதே நேரத்தில் போர்டில் உள்ள பிசினை முழுவதுமாக திடப்படுத்துவதும், மேலும் அகற்றுவதும் ஆகும். பலகையில் எஞ்சியிருக்கும் மன அழுத்தம், பலகை சிதைவதைத் தடுக்கப் பயன்படுகிறது.உதவுதல்.தற்போது, பல இரட்டை பக்க மற்றும் பல அடுக்கு பலகைகள் இன்னும் பேக்கிங்கிற்கு முன் அல்லது பின் பேக்கிங் படியை கடைபிடிக்கின்றன.இருப்பினும், சில தட்டு தொழிற்சாலைகளுக்கு விதிவிலக்குகள் உள்ளன.பல்வேறு PCB தொழிற்சாலைகளின் தற்போதைய PCB உலர்த்தும் நேர விதிமுறைகளும் 4 முதல் 10 மணிநேரம் வரை சீரற்றதாக உள்ளன.தயாரிக்கப்பட்ட அச்சிடப்பட்ட பலகையின் தரம் மற்றும் வார்பேஜிற்கான வாடிக்கையாளரின் தேவைகளுக்கு ஏற்ப முடிவு செய்ய பரிந்துரைக்கப்படுகிறது.ஒரு ஜிக்சாவில் வெட்டப்பட்ட பிறகு அல்லது முழு தொகுதியும் சுடப்பட்ட பிறகு சுடவும்.இரண்டு முறைகளும் சாத்தியமானவை.வெட்டப்பட்ட பிறகு பலகையை சுட பரிந்துரைக்கப்படுகிறது.உள் அடுக்கு பலகையையும் சுட வேண்டும்... 10. லேமினேஷனுக்குப் பிறகு மன அழுத்தம் கூடுதலாக: பல அடுக்கு பலகையை சூடாக அழுத்தி, குளிர்ச்சியாக அழுத்திய பிறகு, அதை வெளியே எடுத்து, வெட்டி அல்லது அரைத்து, பின்னர் 150 டிகிரி செல்சியஸ் வெப்பநிலையில் 4 மணி நேரம் அடுப்பில் தட்டையாக வைக்கவும், இதனால் போர்டில் உள்ள அழுத்தம் இருக்கும். படிப்படியாக வெளியிடப்பட்டது மற்றும் பிசின் முற்றிலும் குணப்படுத்தப்படுகிறது.இந்த நடவடிக்கையை தவிர்க்க முடியாது.
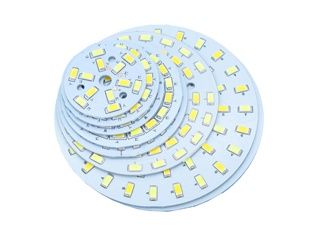
11. மின்முலாம் பூசும்போது மெல்லிய தட்டு நேராக்கப்பட வேண்டும்: 0.4 ~ 0.6 மிமீ அல்ட்ரா-மெல்லிய பல அடுக்கு பலகை மேற்பரப்பு மின்முலாம் மற்றும் வடிவ மின்முலாம் பயன்படுத்தப்படும் போது, சிறப்பு கிளாம்பிங் உருளைகள் செய்யப்பட வேண்டும்.தன்னியக்க மின்முலாம் பூசுதல் கோட்டில் பறக்கும் பேருந்தில் மெல்லிய தகடு இறுகப் பட்ட பிறகு, முழுப் பறக்கும் பேருந்தையும் இறுக்க ஒரு வட்டக் குச்சி பயன்படுத்தப்படுகிறது.உருளைகளில் உள்ள அனைத்து தட்டுகளையும் நேராக்க உருளைகள் ஒன்றாக இணைக்கப்பட்டுள்ளன, இதனால் முலாம் பூசப்பட்ட பின் தட்டுகள் சிதைந்துவிடாது.இந்த அளவு இல்லாமல், 20 முதல் 30 மைக்ரான் செப்பு அடுக்கை மின் முலாம் பூசிய பிறகு, தாள் வளைந்து, அதை சரிசெய்வது கடினம். 12. சூடான காற்றை சமன் செய்த பிறகு பலகையின் குளிர்ச்சி: அச்சிடப்பட்ட பலகை சூடான காற்றால் சமன் செய்யப்படும்போது, சாலிடர் குளியல் (சுமார் 250 டிகிரி செல்சியஸ்) அதிக வெப்பநிலையால் பாதிக்கப்படுகிறது.வெளியே எடுக்கப்பட்ட பிறகு, அது இயற்கையான குளிர்ச்சிக்காக ஒரு தட்டையான பளிங்கு அல்லது எஃகு தகட்டின் மீது வைக்கப்பட வேண்டும், பின்னர் அதை சுத்தம் செய்ய பிந்தைய செயலாக்க இயந்திரத்திற்கு அனுப்ப வேண்டும்.போர்டின் போர்வைத் தடுக்க இது நல்லது.சில தொழிற்சாலைகளில், லீட்-டின் மேற்பரப்பின் பிரகாசத்தை அதிகரிக்க, பலகைகள் சூடான காற்றை சமன் செய்த உடனேயே குளிர்ந்த நீரில் போடப்படுகின்றன, பின்னர் பிந்தைய செயலாக்கத்திற்காக சில நொடிகளுக்குப் பிறகு வெளியே எடுக்கப்படுகின்றன.இந்த வகையான சூடான மற்றும் குளிர் தாக்கம் சில வகையான பலகைகளில் சிதைவை ஏற்படுத்தலாம்.முறுக்கப்பட்ட, அடுக்கு அல்லது கொப்புளங்கள்.கூடுதலாக, குளிரூட்டலுக்கான உபகரணங்களில் காற்று மிதக்கும் படுக்கையை நிறுவலாம். 13. சிதைந்த பலகையின் சிகிச்சை: நன்கு நிர்வகிக்கப்படும் தொழிற்சாலையில், இறுதி ஆய்வின் போது அச்சிடப்பட்ட பலகை 100% பிளாட்னெஸ் சரிபார்க்கப்படும்.அனைத்து தகுதியற்ற பலகைகளும் எடுக்கப்பட்டு, அடுப்பில் வைக்கப்பட்டு, 150 டிகிரி செல்சியஸ் வெப்பநிலையில் 3-6 மணி நேரம் கடுமையான அழுத்தத்தில் சுடப்பட்டு, கடுமையான அழுத்தத்தில் இயற்கையாக குளிர்விக்கப்படும்.பின்னர் பலகையை வெளியே எடுப்பதற்கான அழுத்தத்தைக் குறைத்து, தட்டையான தன்மையைச் சரிபார்க்கவும், இதனால் பலகையின் ஒரு பகுதியை சேமிக்க முடியும், மேலும் சில பலகைகளை சமன் செய்வதற்கு முன் இரண்டு அல்லது மூன்று முறை சுட வேண்டும்.மேற்கூறிய வார்ப்பிங் எதிர்ப்பு செயல்முறை நடவடிக்கைகள் செயல்படுத்தப்படாவிட்டால், சில பலகைகள் பயனற்றதாகிவிடும், மேலும் அவை அகற்றப்படும்.