SMT( Montaxe de placa de circuíto impreso , PCBA ) tamén se denomina tecnoloxía de montaxe en superficie.Durante o proceso de fabricación, a pasta de soldadura quéntase e fúndese nun ambiente de calefacción, de modo que as almofadas de PCB combínanse de forma fiable con compoñentes de montaxe en superficie a través da aliaxe de pasta de soldadura.Chamámoslle a este proceso soldadura por refluxo.A maioría das placas de circuíto son propensas a dobrarse e deformarse cando se someten a Reflow (soldadura por refluxo).En casos graves, incluso pode causar compoñentes como soldaduras baleiras e lápidas. Na liña de montaxe automatizada, se o PCB da fábrica de placas de circuíto non é plano, provocará un posicionamento inexacto, os compoñentes non se poden inserir nos orificios e nas almofadas de montaxe en superficie da placa, e mesmo a máquina de inserción automática estará danada.O taboleiro cos compoñentes está dobrado despois da soldadura e os pés dos compoñentes son difíciles de cortar ordenadamente.A placa non se pode instalar no chasis nin no enchufe dentro da máquina, polo que tamén é moi molesto para a planta de montaxe atoparse coa deformación da tarxeta.Na actualidade, as placas impresas entraron na era do montaxe en superficie e do montaxe de chips, e as plantas de montaxe deben ter requisitos cada vez máis estritos para a deformación das placas.
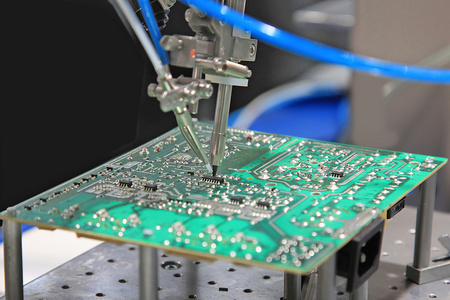
Segundo o US IPC-6012 (edición de 1996) "Especificación e especificación de rendemento para Tableros impresos rígidos ", a deformación e distorsión máxima permitida para placas impresas montadas en superficie é do 0,75 % e do 1,5 % para outras placas. En comparación co IPC-RB-276 (edición de 1992), isto mellorou os requisitos para as placas impresas montadas en superficie. presente, a deformación permitida por varias plantas de montaxe electrónica, independentemente da dobre cara ou multicapa, de 1,6 mm de espesor, adoita ser de 0,70 ~ 0,75%.
Para moitas placas SMT e BGA, o requisito é do 0,5%.Algunhas fábricas de electrónica instan a aumentar o estándar de deformación ata o 0,3%.O método de proba de deformación está de acordo co GB4677.5-84 ou IPC-TM-650.2.4.22B.Coloque o taboleiro impreso na plataforma verificada, insira o pin de proba no lugar onde o grao de deformación é maior e divida o diámetro do pin de proba pola lonxitude do bordo curvo do taboleiro impreso para calcular a deformación do taboleiro. pizarra impresa.A curvatura desapareceu.

Polo tanto, no proceso de fabricación de PCB, cales son as razóns da flexión e deformación da táboa?
A causa de cada flexión e deformación da placa pode ser diferente, pero todo debe atribuírse á tensión aplicada á placa que é maior que a tensión que pode soportar o material da placa.Cando a placa está sometida a unha tensión desigual ou cando a capacidade de cada lugar da placa para resistir a tensión é desigual, o resultado da flexión da placa e a deformación da placa producirase.O seguinte é un resumo das catro causas principais da flexión da placa e a deformación da placa.
1. A superficie de cobre desigual da placa de circuíto empeorará a flexión e deformación da placa.
Xeralmente, unha gran área de folla de cobre está deseñada na placa de circuíto con fins de conexión a terra.Ás veces tamén se deseña unha gran área de folla de cobre na capa de Vcc.Cando estas follas de cobre de gran área non se poden distribuír uniformemente na mesma placa de circuíto Neste momento, provocará o problema de absorción de calor desigual e disipación de calor.Por suposto, a placa de circuíto tamén se expandirá e contraerá coa calor.Se a expansión e a contracción non se poden realizar ao mesmo tempo, provocará diferentes tensións e deformacións.Neste momento, se a temperatura da tarxeta alcanzou Tg O límite superior do valor, a tarxeta comezará a suavizar, causando unha deformación permanente.
2. O peso da propia placa de circuíto fará que a placa se abolle e se deforme
Xeralmente, o forno de refluxo usa unha cadea para impulsar a placa de circuíto cara adiante no forno de refluxo, é dicir, os dous lados da placa utilízanse como fulcros para soportar toda a placa.Se hai pezas pesadas no taboleiro ou o tamaño do taboleiro é demasiado grande, mostrará unha depresión no medio debido á cantidade de sementes, facendo que a placa se dobra.
3. A profundidade do corte en V e da tira de conexión afectarán á deformación da serra de calar
Basicamente, V-Cut é o culpable que destrúe a estrutura do taboleiro, porque V-Cut corta ranuras en forma de V na folla grande orixinal, polo que o V-Cut é propenso a deformarse.
4. Os puntos de conexión (vías) de cada capa da placa de circuíto limitarán a expansión e contracción da placa.
As placas de circuíto de hoxe son na súa maioría placas de varias capas, e haberá puntos de conexión tipo remaches (vía) entre capas.Os puntos de conexión divídense en buratos pasantes, buratos cegos e buratos enterrados.Cando existan puntos de conexión, o taboleiro estará restrinxido.O efecto da expansión e contracción tamén provocará indirectamente a flexión da placa e a deformación da placa.
Entón, como podemos evitar mellor o problema da deformación da tarxeta durante o proceso de fabricación? Aquí tes algúns métodos eficaces que espero que poidan axudarche.
1. Reducir o efecto da temperatura sobre o estrés do taboleiro
Dado que a "temperatura" é a principal fonte de estrés da placa, sempre que se rebaixa a temperatura do forno de refluxo ou a velocidade de quecemento e arrefriamento da placa no forno de refluxo, a aparición de flexión e deformación da placa pode ser moito. reducido.Non obstante, poden producirse outros efectos secundarios, como un curtocircuíto de soldadura.
2. Usando folla de alta Tg
Tg é a temperatura de transición vítrea, é dicir, a temperatura á que o material cambia do estado de vidro ao estado de caucho.Canto menor sexa o valor Tg do material, máis rápido comezará a suavizar o taboleiro despois de entrar no forno de refluxo e o tempo que tarda en converterse en estado de goma branda. Tamén se fará máis longo e, por suposto, a deformación da tarxeta será máis grave. .O uso dunha folla de Tg maior pode aumentar a súa capacidade de soportar tensión e deformación, pero o prezo do material relativo tamén é maior.

3. Aumenta o grosor da placa de circuíto Para conseguir o propósito de ser máis lixeiro e fino para moitos produtos electrónicos, o grosor do taboleiro deixou 1,0 mm, 0,8 mm ou mesmo 0,6 mm.Tal espesor debe evitar que a placa se deforme despois do forno de refluxo, o que é realmente difícil.Recoméndase que, se non hai requisitos de lixeireza e delgadez, o grosor da placa debe ser de 1,6 mm, o que pode reducir moito o risco de dobrar e deformar a placa. 4. Reducir o tamaño da placa de circuíto e reducir o número de crebacabezas Dado que a maioría dos fornos de refluxo usan cadeas para impulsar a placa de circuíto cara adiante, canto maior sexa o tamaño da placa de circuíto será debido ao seu propio peso, abolladura e deformación no forno de refluxo, así que intente poñer o lado longo da placa de circuíto. como o bordo do taboleiro.Na cadea do forno de refluxo pódese reducir a depresión e a deformación causadas polo peso da placa de circuíto.Neste motivo tamén se basea a redución do número de paneis.É dicir, ao pasar o forno, intente utilizar o bordo estreito para pasar a dirección do forno o máis lonxe posible.A cantidade de deformación da depresión. 5. Accesorio de bandexa do forno usado Se os métodos anteriores son difíciles de conseguir, o último é usar o portador/plantilla de refluxo para reducir a cantidade de deformación.O motivo polo que o portador/plantilla de refluxo pode reducir a flexión da placa é porque se espera que se trate de expansión térmica ou contracción en frío.A bandexa pode conter a placa de circuíto e esperar ata que a temperatura da placa de circuíto sexa inferior ao valor Tg e comece a endurecerse de novo, e tamén pode manter o tamaño orixinal. Se o palé dunha soa capa non pode reducir a deformación da placa de circuíto, debe engadirse unha tapa para fixar a placa de circuíto cos palés superior e inferior.Isto pode reducir moito o problema da deformación da placa de circuíto a través do forno de refluxo.Non obstante, esta bandexa do forno é bastante cara e requírese man de obra manual para colocar e reciclar as bandexas. 6. Use Router en lugar de V-Cut para usar a placa secundaria Dado que V-Cut destruirá a resistencia estrutural da placa entre as placas de circuíto, intente non usar a subplaca V-Cut nin reducir a profundidade do V-Cut.
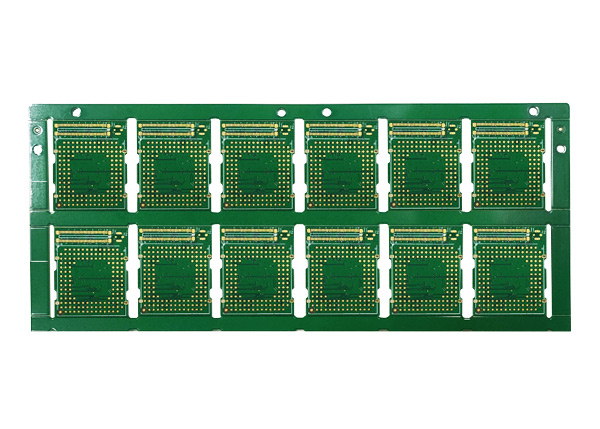
7. Tres puntos percorridos no deseño de enxeñería: A. A disposición dos preimpregnados entre capas debe ser simétrica, por exemplo, para placas de seis capas, o grosor entre 1 ~ 2 e 5 ~ 6 capas e o número de preimpregnados debe ser o mesmo, se non, é fácil deformarse despois da laminación. B. A tarxeta de núcleo multicapa e o preimpregnado deben usar os produtos do mesmo provedor. C. A área do patrón do circuíto no lado A e no lado B da capa exterior debe estar o máis próxima posible.Se o lado A é unha gran superficie de cobre e o lado B só ten algunhas liñas, este tipo de tarxeta impresa deformarase facilmente despois do gravado.Se a área das liñas dos dous lados é demasiado diferente, pode engadir algunhas reixas independentes no lado fino para o equilibrio. 8. A latitude e lonxitude do preimpregnado: Despois de laminar o preimpregnado, as taxas de contracción da urdimbre e da trama son diferentes, e as direccións de urdimbre e trama deben distinguirse durante o corte e a laminación.En caso contrario, é fácil que a placa acabada se deforme despois da laminación e é difícil corrixila aínda que se aplique presión á táboa de cocción.Moitas razóns para a deformación do taboleiro multicapa son que os preimpregnados non se distinguen nas direccións de urdimbre e trama durante a laminación, e que se apilan ao azar. O método para distinguir as direccións de urdimbre e trama: a dirección de laminación do preimpregnado nun rolo é a dirección de urdimbre, mentres que a dirección da anchura é a dirección da trama;para a placa de folla de cobre, o lado longo é a dirección da trama e o lado curto é a dirección da urdidura.Se non está seguro, póñase en contacto co fabricante ou co provedor. 9. Taboleiro de cocer antes de cortar: O propósito de cocer o taboleiro antes de cortar o laminado revestido de cobre (150 graos centígrados, tempo 8 ± 2 horas) é eliminar a humidade do taboleiro e, ao mesmo tempo, facer que a resina do taboleiro se solidifique completamente e eliminar aínda máis o tensión restante no taboleiro, o que é útil para evitar que o taboleiro se deforme.Axudando.Na actualidade, moitas placas de dobre cara e de varias capas aínda se adhiren ao paso de cocción antes ou despois do en branco.Non obstante, hai excepcións para algunhas fábricas de placas.As regulacións actuais de tempo de secado de PCB de varias fábricas de PCB tamén son inconsistentes, que van de 4 a 10 horas.Recoméndase decidir segundo o grao do taboleiro impreso producido e os requisitos do cliente para a deformación.Ás despois de cortar nun rompecabezas ou desfacer despois de cocer todo o bloque.Ambos métodos son factibles.Recoméndase cocer a táboa despois de cortar.O taboleiro da capa interna tamén debe ser cocido... 10. Ademais do estrés despois da laminación: Despois de que o taboleiro de varias capas se preme en quente e en frío, sácase, córtase ou tritúrase as rebabas e, a continuación, colócase nun forno a 150 graos centígrados durante 4 horas, para que o estrés no taboleiro sexa inferior. liberarse gradualmente e a resina está completamente curada.Non se pode omitir este paso.
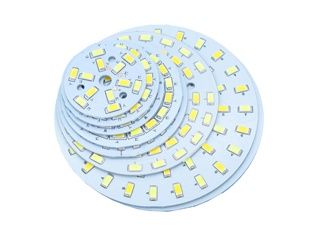
11. A placa delgada debe ser endereitada durante a galvanoplastia: Cando se usa a placa multicapa ultrafina de 0,4 ~ 0,6 mm para a galvanoplastia superficial e a galvanoplastia de patróns, débense fabricar rolos de suxeición especiais.Despois de suxeitar a placa delgada no bus de moscas na liña de galvanoplastia automática, utilízase unha vara redonda para suxeitar todo o autobús de moscas.Os rolos están encordados para endereitar todas as placas dos rolos para que as placas despois do chapado non se deformen.Sen esta medida, despois de galvanoplastia unha capa de cobre de 20 a 30 micras, a chapa dobrarase e é difícil remedialo. 12. Arrefriamento da placa despois da nivelación de aire quente: Cando o taboleiro impreso é nivelado polo aire quente, vese afectado pola alta temperatura do baño de soldadura (uns 250 graos Celsius).Despois de ser retirado, débese colocar sobre unha placa plana de mármore ou aceiro para o arrefriamento natural e despois envialo a unha máquina de postprocesamento para a súa limpeza.Isto é bo para evitar a deformación do taboleiro.Nalgunhas fábricas, para mellorar o brillo da superficie de chumbo-estaño, as placas colócanse en auga fría inmediatamente despois de que se nivele o aire quente e sácanse despois duns segundos para o procesamento posterior.Este tipo de impacto quente e frío pode causar deformacións en certos tipos de táboas.Retorcido, estratificado ou ampolla.Ademais, pódese instalar unha cama de flotación de aire no equipo para o arrefriamento. 13. Tratamento do taboleiro deformado: Nunha fábrica ben xestionada, a placa impresa comprobarase o 100% da planitude durante a inspección final.Todas as placas non cualificadas serán recollidas, introducidas no forno, cocidas a 150 graos centígrados a forte presión durante 3-6 horas e arrefriadas de forma natural a forte presión.A continuación, alivie a presión para sacar o taboleiro e comprobe a planitude, para que se poida gardar parte do taboleiro, e algunhas placas deben ser cocidas e presionadas dúas ou tres veces antes de que se poidan nivelar.Se non se aplican as medidas do proceso antideformación antes mencionadas, algunhas das placas serán inútiles e só poderán ser desguazadas.