SMT( પ્રિન્ટેડ સર્કિટ બોર્ડ એસેમ્બલી , PCBA ) સપાટી માઉન્ટ ટેકનોલોજી પણ કહેવાય છે.ઉત્પાદન પ્રક્રિયા દરમિયાન, સોલ્ડર પેસ્ટ ગરમ થાય છે અને ગરમ વાતાવરણમાં પીગળી જાય છે, જેથી પીસીબી પેડ્સ સોલ્ડર પેસ્ટ એલોય દ્વારા સપાટી માઉન્ટ ઘટકો સાથે વિશ્વસનીય રીતે જોડાય છે.અમે આ પ્રક્રિયાને રિફ્લો સોલ્ડરિંગ કહીએ છીએ.રિફ્લો (રિફ્લો સોલ્ડરિંગ)માંથી પસાર થઈ રહ્યા હોય ત્યારે મોટાભાગના સર્કિટ બોર્ડ બોર્ડ બેન્ડિંગ અને વાર્પિંગ માટે સંવેદનશીલ હોય છે.ગંભીર કિસ્સાઓમાં, તે ખાલી સોલ્ડરિંગ અને ટોમ્બસ્ટોન્સ જેવા ઘટકોનું કારણ બની શકે છે. ઓટોમેટેડ એસેમ્બલી લાઇનમાં, જો સર્કિટ બોર્ડ ફેક્ટરીનું PCB ફ્લેટ ન હોય, તો તે અચોક્કસ સ્થિતિનું કારણ બને છે, બોર્ડના છિદ્રો અને સપાટીના માઉન્ટ પેડ્સમાં ઘટકો દાખલ કરી શકાતા નથી, અને સ્વચાલિત નિવેશ મશીનને પણ નુકસાન થશે.ઘટકો સાથેનું બોર્ડ વેલ્ડીંગ પછી વળેલું છે, અને ઘટક ફીટને સરસ રીતે કાપવા મુશ્કેલ છે.મશીનની અંદરના ચેસીસ અથવા સોકેટ પર બોર્ડ ઇન્સ્ટોલ કરી શકાતું નથી, તેથી એસેમ્બલી પ્લાન્ટ માટે પણ બોર્ડ વાર્નિંગનો સામનો કરવો ખૂબ જ હેરાન કરે છે.હાલમાં, પ્રિન્ટેડ બોર્ડ સરફેસ માઉન્ટિંગ અને ચિપ માઉન્ટિંગના યુગમાં પ્રવેશી ચૂક્યા છે, અને એસેમ્બલી પ્લાન્ટ્સમાં બોર્ડ વોર્પિંગ માટે સખત અને કડક આવશ્યકતાઓ હોવી આવશ્યક છે.
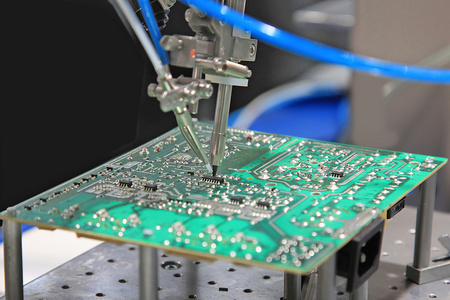
યુએસ IPC-6012 (1996 આવૃત્તિ) અનુસાર "વિશિષ્ટતા અને પ્રદર્શન સ્પષ્ટીકરણ માટે સખત મુદ્રિત બોર્ડ ", સરફેસ-માઉન્ટેડ પ્રિન્ટેડ બોર્ડ્સ માટે મહત્તમ સ્વીકાર્ય વોરપેજ અને વિકૃતિ 0.75% છે, અને અન્ય બોર્ડ માટે 1.5% છે. IPC-RB-276 (1992 આવૃત્તિ) ની તુલનામાં, આનાથી સરફેસ-માઉન્ટેડ પ્રિન્ટેડ બોર્ડ માટેની આવશ્યકતાઓમાં સુધારો થયો છે. હાલમાં, વિવિધ ઇલેક્ટ્રોનિક એસેમ્બલી પ્લાન્ટ્સ દ્વારા મંજૂર કરાયેલ વોરપેજ, ડબલ-સાઇડ અથવા મલ્ટિ-લેયર, 1.6mm જાડાઈને ધ્યાનમાં લીધા વિના, સામાન્ય રીતે 0.70~0.75% છે.
ઘણા SMT અને BGA બોર્ડ માટે, જરૂરિયાત 0.5% છે.કેટલીક ઈલેક્ટ્રોનિક ફેક્ટરીઓ વોરપેજનું ધોરણ વધારીને 0.3% કરવા વિનંતી કરી રહી છે.વોરપેજનું પરીક્ષણ કરવાની પદ્ધતિ GB4677.5-84 અથવા IPC-TM-650.2.4.22B અનુસાર છે.પ્રિન્ટેડ બોર્ડને વેરિફાઈડ પ્લેટફોર્મ પર મૂકો, ટેસ્ટ પિનને તે જગ્યાએ દાખલ કરો જ્યાં વોરપેજની ડિગ્રી સૌથી મોટી હોય અને ટેસ્ટ પિનના વ્યાસને પ્રિન્ટેડ બોર્ડની વક્ર ધારની લંબાઈથી વિભાજીત કરો. મુદ્રિત બોર્ડ.વક્રતા ગઈ.

તેથી PCB ઉત્પાદનની પ્રક્રિયામાં, બોર્ડના વાળવા અને લપેટવાના કારણો શું છે?
દરેક પ્લેટ બેન્ડિંગ અને પ્લેટ લૅપિંગનું કારણ અલગ-અલગ હોઈ શકે છે, પરંતુ તે બધા પ્લેટ પર લાગુ પડતા તણાવને આભારી હોવા જોઈએ જે પ્લેટ સામગ્રીનો સામનો કરી શકે તેવા તણાવ કરતા વધારે છે.જ્યારે પ્લેટ અસમાન તાણને આધિન હોય અથવા જ્યારે બોર્ડ પરના દરેક સ્થાનની તાણનો પ્રતિકાર કરવાની ક્ષમતા અસમાન હોય, ત્યારે બોર્ડના બેન્ડિંગ અને બોર્ડના વિકૃતિનું પરિણામ આવશે.નીચે પ્લેટ બેન્ડિંગ અને પ્લેટ વોરિંગના ચાર મુખ્ય કારણોનો સારાંશ છે.
1. સર્કિટ બોર્ડ પર અસમાન તાંબાની સપાટીનો વિસ્તાર બોર્ડના બેન્ડિંગ અને વાર્નિંગને વધુ ખરાબ કરશે
સામાન્ય રીતે, ગ્રાઉન્ડિંગ હેતુઓ માટે સર્કિટ બોર્ડ પર કોપર ફોઇલનો મોટો વિસ્તાર ડિઝાઇન કરવામાં આવે છે.કેટલીકવાર વીસીસી લેયર પર કોપર ફોઇલનો મોટો વિસ્તાર પણ ડિઝાઇન કરવામાં આવે છે.જ્યારે આ મોટા વિસ્તારના કોપર ફોઇલ્સ સમાન સર્કિટ બોર્ડ પર સમાનરૂપે વિતરિત કરી શકાતા નથી, ત્યારે તે અસમાન ગરમી શોષણ અને ગરમીના વિસર્જનની સમસ્યાનું કારણ બનશે.અલબત્ત, સર્કિટ બોર્ડ પણ વિસ્તરણ કરશે અને ગરમી સાથે સંકોચન કરશે.જો વિસ્તરણ અને સંકોચન એક જ સમયે કરી શકાતા નથી, તો તે વિવિધ તાણ અને વિકૃતિનું કારણ બનશે.આ સમયે, જો બોર્ડનું તાપમાન Tg મૂલ્યની ઉપલી મર્યાદા સુધી પહોંચી ગયું હોય, તો બોર્ડ નરમ થવાનું શરૂ કરશે, જેના કારણે કાયમી વિકૃતિ થશે.
2. સર્કિટ બોર્ડનું વજન પોતે જ બોર્ડને ડેન્ટ અને વિકૃત કરશે
સામાન્ય રીતે, રિફ્લો ફર્નેસ સર્કિટ બોર્ડને રિફ્લો ફર્નેસમાં આગળ ચલાવવા માટે સાંકળનો ઉપયોગ કરે છે, એટલે કે, સમગ્ર બોર્ડને ટેકો આપવા માટે બોર્ડની બે બાજુઓ ફુલક્રમ તરીકે ઉપયોગમાં લેવાય છે.જો બોર્ડ પર ભારે ભાગો હોય, અથવા બોર્ડનું કદ ખૂબ મોટું હોય, તો તે બીજના જથ્થાને કારણે મધ્યમાં મંદી બતાવશે, જેના કારણે પ્લેટને વળાંક આવે છે.
3. વી-કટની ઊંડાઈ અને કનેક્ટિંગ સ્ટ્રીપ જીગ્સૉના વિરૂપતાને અસર કરશે
મૂળભૂત રીતે, વી-કટ એ ગુનેગાર છે જે બોર્ડની રચનાને નષ્ટ કરે છે, કારણ કે વી-કટ મૂળ મોટી શીટ પર વી-આકારના ગ્રુવ્સને કાપી નાખે છે, તેથી વી-કટ વિકૃતિની સંભાવના ધરાવે છે.
4. સર્કિટ બોર્ડ પરના દરેક સ્તરના કનેક્શન પોઈન્ટ્સ (વિઆસ) બોર્ડના વિસ્તરણ અને સંકોચનને મર્યાદિત કરશે.
આજના સર્કિટ બોર્ડ મોટે ભાગે મલ્ટિ-લેયર બોર્ડ છે, અને સ્તરો વચ્ચે રિવેટ જેવા કનેક્શન પોઈન્ટ (વાયા) હશે.કનેક્શન પોઈન્ટને છિદ્રો, અંધ છિદ્રો અને દફનાવવામાં આવેલા છિદ્રો દ્વારા વિભાજિત કરવામાં આવે છે.જ્યાં કનેક્શન પોઇન્ટ હશે ત્યાં બોર્ડ પ્રતિબંધિત રહેશે.વિસ્તરણ અને સંકોચનની અસર પણ આડકતરી રીતે પ્લેટ બેન્ડિંગ અને પ્લેટ વિરિંગનું કારણ બનશે.
તો મેન્યુફેક્ચરિંગ પ્રક્રિયા દરમિયાન બોર્ડના વિકૃતિની સમસ્યાને આપણે કેવી રીતે વધુ સારી રીતે અટકાવી શકીએ? અહીં કેટલીક અસરકારક પદ્ધતિઓ છે જે મને આશા છે કે તમને મદદ કરી શકે છે.
1. બોર્ડના તાણ પર તાપમાનની અસરમાં ઘટાડો
"તાપમાન" એ બોર્ડના તાણનો મુખ્ય સ્ત્રોત હોવાથી, જ્યાં સુધી રિફ્લો ઓવનનું તાપમાન ઓછું કરવામાં આવે અથવા રિફ્લો ઓવનમાં બોર્ડને ગરમ અને ઠંડકનો દર ધીમો કરવામાં આવે, ત્યાં સુધી પ્લેટ બેન્ડિંગ અને વોરપેજની ઘટનાઓ મોટા પ્રમાણમાં થઈ શકે છે. ઘટાડોજો કે, અન્ય આડઅસર થઈ શકે છે, જેમ કે સોલ્ડર શોર્ટ સર્કિટ.
2. ઉચ્ચ ટીજી શીટનો ઉપયોગ કરવો
Tg એ કાચનું સંક્રમણ તાપમાન છે, એટલે કે તે તાપમાન કે જેના પર સામગ્રી કાચની સ્થિતિમાંથી રબરની સ્થિતિમાં બદલાય છે.સામગ્રીનું Tg મૂલ્ય જેટલું ઓછું હશે, રિફ્લો ઓવનમાં પ્રવેશ્યા પછી બોર્ડ જેટલી ઝડપથી નરમ થવાનું શરૂ કરે છે, અને નરમ રબરની સ્થિતિમાં જેટલો સમય લાગશે તે પણ લાંબો થશે, અને બોર્ડની વિકૃતિ અલબત્ત વધુ ગંભીર હશે. .ઉચ્ચ ટીજી શીટનો ઉપયોગ તણાવ અને વિકૃતિનો સામનો કરવાની તેની ક્ષમતામાં વધારો કરી શકે છે, પરંતુ સંબંધિત સામગ્રીની કિંમત પણ વધારે છે.

3. સર્કિટ બોર્ડની જાડાઈમાં વધારો ઘણા ઇલેક્ટ્રોનિક ઉત્પાદનો માટે હળવા અને પાતળાના હેતુને હાંસલ કરવા માટે, બોર્ડની જાડાઈ 1.0mm, 0.8mm અથવા તો 0.6mm છોડી દીધી છે.આવી જાડાઈએ બોર્ડને રિફ્લો ફર્નેસ પછી વિકૃત થતું અટકાવવું જોઈએ, જે ખરેખર મુશ્કેલ છે.એવી ભલામણ કરવામાં આવે છે કે જો હળવાશ અને પાતળાપણું માટે કોઈ આવશ્યકતા નથી, તો બોર્ડની જાડાઈ 1.6mm હોવી જોઈએ, જે બોર્ડના વળાંક અને વિકૃતિના જોખમને મોટા પ્રમાણમાં ઘટાડી શકે છે. 4. સર્કિટ બોર્ડનું કદ ઘટાડવું અને કોયડાઓની સંખ્યા ઘટાડવી મોટાભાગની રિફ્લો ફર્નેસ સર્કિટ બોર્ડને આગળ ચલાવવા માટે સાંકળોનો ઉપયોગ કરતી હોવાથી, સર્કિટ બોર્ડનું કદ જેટલું મોટું હશે તે તેના પોતાના વજન, ડેન્ટ અને રિફ્લો ફર્નેસમાં વિકૃતિને કારણે હશે, તેથી સર્કિટ બોર્ડની લાંબી બાજુ મૂકવાનો પ્રયાસ કરો. બોર્ડની ધાર તરીકે.રિફ્લો ફર્નેસની સાંકળ પર, સર્કિટ બોર્ડના વજનને કારણે ડિપ્રેશન અને વિરૂપતા ઘટાડી શકાય છે.પેનલની સંખ્યામાં ઘટાડો પણ આ કારણ પર આધારિત છે.કહેવાનો અર્થ એ છે કે ભઠ્ઠી પસાર કરતી વખતે, શક્ય હોય ત્યાં સુધી ભઠ્ઠીની દિશા પસાર કરવા માટે સાંકડી ધારનો ઉપયોગ કરવાનો પ્રયાસ કરો.ડિપ્રેશન વિરૂપતા જથ્થો. 5. વપરાયેલ ફર્નેસ ટ્રે ફિક્સ્ચર જો ઉપરોક્ત પદ્ધતિઓ હાંસલ કરવી મુશ્કેલ હોય, તો છેલ્લી પદ્ધતિ વિકૃતિની માત્રા ઘટાડવા માટે રિફ્લો કેરિયર/ટેમ્પલેટનો ઉપયોગ કરવાનો છે.રિફ્લો કેરિયર/ટેમ્પલેટ પ્લેટના બેન્ડિંગને ઘટાડી શકે છે તેનું કારણ એ છે કે તે થર્મલ વિસ્તરણ હોય કે ઠંડા સંકોચન હોય.ટ્રે સર્કિટ બોર્ડને પકડી શકે છે અને જ્યાં સુધી સર્કિટ બોર્ડનું તાપમાન Tg મૂલ્ય કરતા ઓછું ન થાય ત્યાં સુધી રાહ જોઈ શકે છે અને ફરીથી સખત થવાનું શરૂ કરે છે, અને તે મૂળ કદ પણ જાળવી શકે છે. જો સિંગલ-લેયર પૅલેટ સર્કિટ બોર્ડના વિરૂપતાને ઘટાડી શકતું નથી, તો સર્કિટ બોર્ડને ઉપલા અને નીચલા પૅલેટ્સ સાથે ક્લેમ્બ કરવા માટે કવર ઉમેરવું આવશ્યક છે.આ રિફ્લો ફર્નેસ દ્વારા સર્કિટ બોર્ડના વિકૃતિની સમસ્યાને મોટા પ્રમાણમાં ઘટાડી શકે છે.જો કે, આ ફર્નેસ ટ્રે ખૂબ ખર્ચાળ છે, અને ટ્રે મૂકવા અને રિસાયકલ કરવા માટે મેન્યુઅલ લેબરની જરૂર પડે છે. 6. સબ-બોર્ડનો ઉપયોગ કરવા V-Cut ને બદલે રાઉટરનો ઉપયોગ કરો V-Cut સર્કિટ બોર્ડ વચ્ચેના બોર્ડની માળખાકીય શક્તિને નષ્ટ કરશે, તેથી V-Cut સબ-બોર્ડનો ઉપયોગ ન કરવાનો પ્રયાસ કરો અથવા V-Cut ની ઊંડાઈ ઓછી કરો.
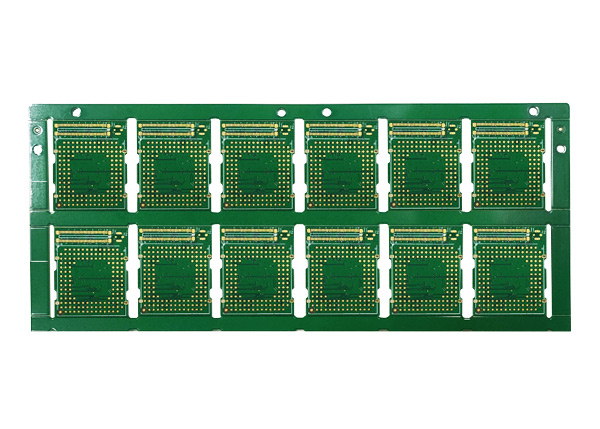
7. એન્જિનિયરિંગ ડિઝાઇનમાં ત્રણ બિંદુઓ ચાલે છે: A. ઇન્ટરલેયર પ્રીપ્રેગની ગોઠવણી સપ્રમાણ હોવી જોઈએ, ઉદાહરણ તરીકે, છ-સ્તરવાળા બોર્ડ માટે, 1~2 અને 5~6 સ્તરો વચ્ચેની જાડાઈ અને પ્રીપ્રેગ્સની સંખ્યા સમાન હોવી જોઈએ, અન્યથા લેમિનેશન પછી તેને વાર્પ કરવું સરળ છે. B. મલ્ટિ-લેયર કોર બોર્ડ અને પ્રિપ્રેગ એ જ સપ્લાયરના ઉત્પાદનોનો ઉપયોગ કરવો જોઈએ. C. બાહ્ય સ્તરની બાજુ A અને બાજુ B પરની સર્કિટ પેટર્નનો વિસ્તાર શક્ય તેટલો નજીક હોવો જોઈએ.જો A બાજુ મોટી તાંબાની સપાટી હોય, અને B બાજુમાં માત્ર થોડી જ રેખાઓ હોય, તો આ પ્રકારનું પ્રિન્ટેડ બોર્ડ એચીંગ કર્યા પછી સરળતાથી લપસી જશે.જો બે બાજુઓ પરની રેખાઓનો વિસ્તાર ઘણો અલગ હોય, તો તમે સંતુલન માટે પાતળી બાજુ પર કેટલીક સ્વતંત્ર ગ્રીડ ઉમેરી શકો છો. 8. પ્રિપ્રેગનું અક્ષાંશ અને રેખાંશ: પ્રીપ્રેગને લેમિનેટ કર્યા પછી, વાર્પ અને વેફ્ટ સંકોચન દર અલગ હોય છે, અને બ્લેન્કિંગ અને લેમિનેશન દરમિયાન વાર્પ અને વેફ્ટ દિશાઓને અલગ પાડવી આવશ્યક છે.નહિંતર, લેમિનેશન પછી ફિનિશ્ડ બોર્ડને લપેટવું સરળ છે, અને જો બેકિંગ બોર્ડ પર દબાણ લાગુ કરવામાં આવે તો પણ તેને સુધારવું મુશ્કેલ છે.મલ્ટિલેયર બોર્ડના વોરપેજના ઘણા કારણો એ છે કે લેમિનેશન દરમિયાન પ્રીપ્રેગ્સને વાર્પ અને વેફ્ટ દિશામાં અલગ પાડવામાં આવતા નથી, અને તે રેન્ડમ રીતે સ્ટેક કરવામાં આવે છે. વાર્પ અને વેફ્ટ દિશાઓને અલગ પાડવાની પદ્ધતિ: રોલમાં પ્રિપ્રેગની રોલિંગ દિશા એ વાર્પ દિશા છે, જ્યારે પહોળાઈની દિશા વેફ્ટ દિશા છે;કોપર ફોઇલ બોર્ડ માટે, લાંબી બાજુ વેફ્ટ દિશા છે અને ટૂંકી બાજુ તાણની દિશા છે.જો તમને ખાતરી ન હોય, તો કૃપા કરીને ઉત્પાદક અથવા સપ્લાયર ક્વેરીનો સંપર્ક કરો. 9. કાપતા પહેલા બેકિંગ બોર્ડ: કોપર ક્લેડ લેમિનેટ (150 ડિગ્રી સેલ્સિયસ, સમય 8±2 કલાક) કાપતા પહેલા બોર્ડને પકવવાનો હેતુ બોર્ડમાં રહેલા ભેજને દૂર કરવાનો છે, અને તે જ સમયે બોર્ડમાં રહેલા રેઝિનને સંપૂર્ણપણે ઘન બનાવવાનો છે, અને વધુ દૂર કરે છે. બોર્ડમાં બાકી રહેલો તણાવ, જે બોર્ડને લથડતા અટકાવવા માટે ઉપયોગી છે.મદદ કરે છે.હાલમાં, ઘણા ડબલ-સાઇડેડ અને મલ્ટિ-લેયર બોર્ડ હજુ પણ બ્લેન્કિંગ પહેલાં અથવા પછી પકવવાના પગલાને વળગી રહે છે.જો કે, કેટલાક પ્લેટ ફેક્ટરીઓ માટે અપવાદો છે.વિવિધ PCB ફેક્ટરીઓના વર્તમાન PCB સૂકવવાના સમયના નિયમો પણ અસંગત છે, જે 4 થી 10 કલાક સુધીના છે.ઉત્પાદિત પ્રિન્ટેડ બોર્ડના ગ્રેડ અને વોરપેજ માટે ગ્રાહકની જરૂરિયાતો અનુસાર નિર્ણય લેવાની ભલામણ કરવામાં આવે છે.જીગ્સૉમાં કાપ્યા પછી બેક કરો અથવા આખો બ્લોક બેક થઈ જાય પછી બ્લેન્કિંગ કરો.બંને પદ્ધતિઓ શક્ય છે.કાપ્યા પછી બોર્ડને શેકવાની ભલામણ કરવામાં આવે છે.આંતરિક સ્તરનું બોર્ડ પણ શેકવું જોઈએ ... 10. લેમિનેશન પછી તણાવ ઉપરાંત: મલ્ટિ-લેયર બોર્ડને ગરમ-દબાવ્યા પછી અને ઠંડા-દબાવ્યા પછી, તેને બહાર કાઢવામાં આવે છે, બર્સને કાપીને અથવા મિલ્ડ કરવામાં આવે છે, અને પછી તેને 150 ડિગ્રી સેલ્સિયસ પર 4 કલાક માટે પકાવવાની નાની ભઠ્ઠીમાં સપાટ રાખવામાં આવે છે, જેથી બોર્ડમાં તણાવ ઓછો થાય. ધીમે ધીમે મુક્ત થાય છે અને રેઝિન સંપૂર્ણપણે મટાડવામાં આવે છે.આ પગલું અવગણી શકાય નહીં.
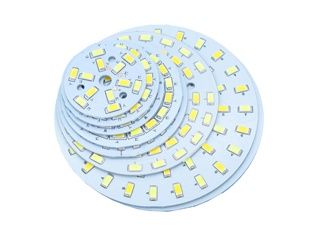
11. ઇલેક્ટ્રોપ્લેટિંગ દરમિયાન પાતળી પ્લેટને સીધી કરવાની જરૂર છે: જ્યારે 0.4~0.6mm અલ્ટ્રા-થિન મલ્ટિલેયર બોર્ડનો ઉપયોગ સપાટીના ઇલેક્ટ્રોપ્લેટિંગ અને પેટર્ન ઇલેક્ટ્રોપ્લેટિંગ માટે કરવામાં આવે છે, ત્યારે ખાસ ક્લેમ્પિંગ રોલર્સ બનાવવા જોઈએ.ઓટોમેટિક ઇલેક્ટ્રોપ્લેટિંગ લાઇન પર ફ્લાય બસ પર પાતળી પ્લેટ ક્લેમ્પ કર્યા પછી, આખી ફ્લાય બસને ક્લેમ્પ કરવા માટે ગોળ લાકડીનો ઉપયોગ કરવામાં આવે છે.રોલરો પરની બધી પ્લેટોને સીધી કરવા માટે રોલર્સને એકસાથે બાંધવામાં આવે છે જેથી પ્લેટિંગ પછીની પ્લેટો વિકૃત ન થાય.આ માપ વિના, 20 થી 30 માઇક્રોનનું તાંબાના સ્તરને ઇલેક્ટ્રોપ્લેટિંગ કર્યા પછી, શીટ વળાંક આવશે અને તેનો ઉપાય કરવો મુશ્કેલ છે. 12. ગરમ હવાના સ્તરીકરણ પછી બોર્ડને ઠંડુ કરવું: જ્યારે પ્રિન્ટેડ બોર્ડ ગરમ હવા દ્વારા સમતળ કરવામાં આવે છે, ત્યારે તે સોલ્ડર બાથના ઊંચા તાપમાન (લગભગ 250 ડિગ્રી સેલ્સિયસ) દ્વારા પ્રભાવિત થાય છે.બહાર કાઢ્યા પછી, તેને કુદરતી ઠંડક માટે સપાટ માર્બલ અથવા સ્ટીલ પ્લેટ પર મૂકવું જોઈએ, અને પછી સફાઈ માટે પોસ્ટ-પ્રોસેસિંગ મશીનમાં મોકલવું જોઈએ.બોર્ડના વોરપેજને રોકવા માટે આ સારું છે.કેટલીક ફેક્ટરીઓમાં, લીડ-ટીનની સપાટીની ચમક વધારવા માટે, ગરમ હવાને સમતળ કર્યા પછી તરત જ બોર્ડને ઠંડા પાણીમાં નાખવામાં આવે છે, અને પછી પોસ્ટ-પ્રોસેસિંગ માટે થોડી સેકંડ પછી બહાર કાઢવામાં આવે છે.આ પ્રકારની ગરમ અને ઠંડીની અસર અમુક પ્રકારના બોર્ડ પર લપેટાઈ શકે છે.ટ્વિસ્ટેડ, સ્તરવાળી અથવા ફોલ્લીઓ.વધુમાં, ઠંડક માટે સાધનો પર એર ફ્લોટેશન બેડ સ્થાપિત કરી શકાય છે. 13. વિકૃત બોર્ડની સારવાર: સારી રીતે સંચાલિત ફેક્ટરીમાં, અંતિમ નિરીક્ષણ દરમિયાન પ્રિન્ટેડ બોર્ડની 100% સપાટતા તપાસવામાં આવશે.તમામ અયોગ્ય બોર્ડને બહાર કાઢવામાં આવશે, પકાવવાની નાની ભઠ્ઠીમાં મૂકવામાં આવશે, 150 ડિગ્રી સેલ્સિયસ પર ભારે દબાણ હેઠળ 3-6 કલાક માટે શેકવામાં આવશે, અને ભારે દબાણ હેઠળ કુદરતી રીતે ઠંડુ કરવામાં આવશે.પછી બોર્ડને બહાર કાઢવાના દબાણને દૂર કરો, અને સપાટતા તપાસો, જેથી બોર્ડનો ભાગ સાચવી શકાય, અને કેટલાક બોર્ડને સમતળ કરવામાં આવે તે પહેલાં તેને બે કે ત્રણ વખત બેક કરીને દબાવવાની જરૂર છે.જો ઉપરોક્ત ઉલ્લેખિત એન્ટિ-વાર્પિંગ પ્રક્રિયાના પગલાં અમલમાં ન આવે તો, કેટલાક બોર્ડ નકામા થઈ જશે અને ફક્ત તેને કાઢી નાખવામાં આવશે.