SMT( මුද්රිත පරිපථ පුවරු එකලස් කිරීම , PCBA ) මතුපිට සවි කිරීමේ තාක්ෂණය ලෙසද හැඳින්වේ.නිෂ්පාදන ක්රියාවලියේදී, පෑස්සුම් පේස්ට් රත් කර උණුසුම් පරිසරයක උණු කරනු ලැබේ, එවිට PCB පෑඩ් විශ්වාසදායක ලෙස පෑස්සුම් පේස්ට් මිශ්ර ලෝහය හරහා මතුපිට සවි කිරීම් සංරචක සමඟ ඒකාබද්ධ වේ.මෙම ක්රියාවලිය අපි reflow soldering ලෙස හඳුන්වමු.බොහෝ පරිපථ පුවරු Reflow (reflow soldering) සිදු කරන විට පුවරු නැමීමට සහ විකෘති වීමට ඉඩ ඇත.දරුණු අවස්ථාවල දී, එය හිස් පෑස්සුම් සහ සොහොන් ගල් වැනි සංරචක වලට පවා හේතු විය හැක. ස්වයංක්රීය එකලස් කිරීමේ රේඛාවේදී, පරිපථ පුවරු කම්හලේ PCB පැතලි නොවේ නම්, එය වැරදි ස්ථානගත කිරීමක් සිදු කරයි, පුවරුවේ සිදුරු සහ මතුපිට සවිකිරීමේ පෑඩ් වලට සංරචක ඇතුළු කළ නොහැක, ස්වයංක්රීය ඇතුළු කිරීමේ යන්ත්රයට පවා හානි සිදු වේ.සංරචක සහිත පුවරුව වෑල්ඩින් කිරීමෙන් පසු නැමී ඇති අතර, සංරචක අඩි පිළිවෙලට කපා ගැනීමට අපහසු වේ.පුවරුව චැසිය මත හෝ යන්ත්රය තුළ ඇති සොකට් එක මත ස්ථාපනය කළ නොහැක, එබැවින් එකලස් කිරීමේ බලාගාරයට පුවරු විකෘති වීම ද ඉතා කරදරකාරී ය.වර්තමානයේ, මුද්රිත පුවරු මතුපිට සවිකිරීමේ සහ චිප් සවිකිරීමේ යුගයට ඇතුල් වී ඇති අතර, පුවරු විකෘති කිරීම සඳහා එකලස් කිරීමේ පැල දැඩි හා දැඩි අවශ්යතා තිබිය යුතුය.
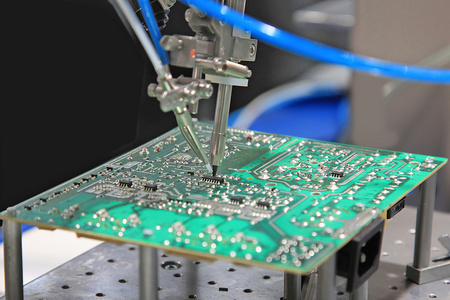
US IPC-6012 (1996 සංස්කරණය) ට අනුව "විශේෂාංග සහ කාර්ය සාධන පිරිවිතර දෘඪ මුද්රිත පුවරු ", මතුපිට සවිකර ඇති මුද්රිත පුවරු සඳහා උපරිම අවසර ලත් යුධ පිටුව සහ විකෘති කිරීම 0.75% වන අතර අනෙකුත් පුවරු සඳහා 1.5% වේ. IPC-RB-276 (1992 සංස්කරණය) සමඟ සසඳන විට, මෙය මතුපිට සවිකර ඇති මුද්රිත පුවරු සඳහා අවශ්යතා වැඩි දියුණු කර ඇත. වර්තමානයේ, ද්වි-පාර්ශ්වික හෝ බහු-ස්ථර, 1.6mm ඝනකම නොතකා, විවිධ ඉලෙක්ට්රොනික එකලස් කිරීමේ කම්හල් මඟින් අවසර දී ඇති යුධ පිටුව සාමාන්යයෙන් 0.70~0.75% වේ.
බොහෝ SMT සහ BGA පුවරු සඳහා, අවශ්යතාවය 0.5% කි.සමහර ඉලෙක්ට්රොනික කර්මාන්තශාලා Warpage ප්රමිතිය 0.3% දක්වා වැඩි කරන ලෙස ඉල්ලා සිටී.යුධ පිටුව පරීක්ෂා කිරීමේ ක්රමය GB4677.5-84 හෝ IPC-TM-650.2.4.22B ට අනුකූල වේ.මුද්රිත පුවරුව සත්යාපිත වේදිකාව මත තබා, යුධ පිටුවේ උපාධිය විශාලතම ස්ථානයට පරීක්ෂණ පින් එක ඇතුළු කරන්න, සහ පරීක්ෂණ පින් එකේ විෂ්කම්භය මුද්රිත පුවරුවේ වක්ර දාරයේ දිගෙන් බෙදන්න. මුද්රිත පුවරුව.වංගුව නැතිවෙලා.

එබැවින් PCB නිෂ්පාදන ක්රියාවලියේදී, පුවරුව නැමීමට සහ විකෘති වීමට හේතු මොනවාද?
එක් එක් තහඩුව නැමීමට සහ තහඩු විකෘති වීමට හේතුව වෙනස් විය හැකි නමුත්, ඒ සියල්ල තහඩු ද්රව්යයට ඔරොත්තු දිය හැකි ආතතියට වඩා වැඩි පීඩනයක් තහඩුවට යොදන ආතතියට ආරෝපණය කළ යුතුය.තහඩුව අසමාන ආතතියට ලක් වූ විට හෝ පුවරුවේ එක් එක් ස්ථානයට ආතතියට ඔරොත්තු දීමේ හැකියාව අසමාන වූ විට, පුවරුව නැමීමේ සහ පුවරු විකෘති වීමේ ප්රතිඵලය සිදුවනු ඇත.පහත දැක්වෙන්නේ තහඩු නැමීමට සහ තහඩු විකෘති වීමට බලපාන ප්රධාන හේතු හතරේ සාරාංශයකි.
1. පරිපථ පුවරුවේ ඇති අසමාන තඹ මතුපිට ප්රදේශය පුවරුවේ නැමීම සහ විකෘති වීම නරක අතට හැරේ
සාමාන්යයෙන්, තඹ තීරු විශාල ප්රදේශයක් භූගත අරමුණු සඳහා පරිපථ පුවරුව මත නිර්මාණය කර ඇත.සමහර විට Vcc ස්තරය මත තඹ තීරු විශාල ප්රදේශයක් ද නිර්මාණය කර ඇත.මෙම විශාල ප්රදේශයේ තඹ තීරු එකම පරිපථ පුවරුවක ඒකාකාරව බෙදා හැරීමට නොහැකි වූ විට, එය අසමාන තාප අවශෝෂණය සහ තාපය විසුරුවා හැරීමේ ගැටලුවට හේතු වේ.ඇත්ත වශයෙන්ම, පරිපථ පුවරුව ද තාපය සමඟ පුළුල් වන අතර හැකිලෙනු ඇත.ප්රසාරණය හා හැකිලීම එකම අවස්ථාවේදීම සිදු කළ නොහැකි නම්, එය විවිධ ආතතිය හා විරූපණයට හේතු වේ.මෙම අවස්ථාවේදී, පුවරුවේ උෂ්ණත්වය Tg අගයෙහි ඉහළ සීමාවට ළඟා වී ඇත්නම්, පුවරුව මෘදු වීමට පටන් ගනී, එය ස්ථිර විරූපණයට හේතු වේ.
2. පරිපථ පුවරුවේ බරම පුවරුව ඩැට් සහ විකෘති වීමට හේතු වේ
සාමාන්යයෙන්, ප්රතිප්රවාහ උදුන මඟින් පරිපථ පුවරුව පෙරට ගෙනයාම සඳහා දාමයක් භාවිතා කරයි, එනම් පුවරුවේ පැති දෙක සම්පූර්ණ පුවරුවට ආධාර කිරීම සඳහා ෆුල්ක්රම් ලෙස භාවිතා කරයි.පුවරුවේ බර කොටස් තිබේ නම් හෝ පුවරුවේ ප්රමාණය ඉතා විශාල නම්, එය බීජ ප්රමාණය නිසා මැද අවපාතයක් පෙන්වයි, එය තහඩුව නැමීමට හේතු වේ.
3. V-කට් එකේ ගැඹුර සහ සම්බන්ධක තීරුව ජිග්සෝවේ විරූපණයට බලපානු ඇත
මූලික වශයෙන්, V-Cut යනු පුවරුවේ ව්යුහය විනාශ කරන වැරදිකරුවා වන අතර, V-Cut මුල් විශාල පත්රයේ V-හැඩැති කට්ට කපන බැවින් V-Cut විරූපණයට ගොදුරු වේ.
4. පරිපථ පුවරුවේ එක් එක් ස්ථරයේ සම්බන්ධක ලක්ෂ්ය (හරහා) පුවරුවේ ප්රසාරණය සහ හැකිලීම සීමා කරනු ඇත
අද පරිපථ පුවරු බොහෝ විට බහු ස්ථර පුවරු වන අතර ස්ථර අතර රිවට් වැනි සම්බන්ධතා ස්ථාන (හරහා) ඇත.සම්බන්ධක ස්ථාන සිදුරු, අන්ධ සිදුරු සහ වළලන ලද සිදුරු හරහා බෙදී ඇත.සම්බන්ධතා ස්ථාන ඇති තැන, පුවරුව සීමා කරනු ලැබේ.ප්රසාරණය සහ හැකිලීමේ බලපෑම ද වක්රව තහඩු නැමීමට සහ තහඩු විකෘති වීමට හේතු වේ.
ඉතින් නිෂ්පාදන ක්රියාවලියේදී පුවරු විකෘති වීමේ ගැටලුව අපට වඩා හොඳින් වළක්වා ගත හැක්කේ කෙසේද? ඔබට උපකාර කළ හැකි යැයි මම බලාපොරොත්තු වන ඵලදායී ක්රම කිහිපයක් මෙන්න.
1. පුවරුවේ ආතතිය මත උෂ්ණත්වයේ බලපෑම අඩු කරන්න
"උෂ්ණත්වය" පුවරු ආතතියේ ප්රධාන ප්රභවය වන බැවින්, ප්රතිප්රවාහ උඳුනේ උෂ්ණත්වය පහත හෙලන තාක් හෝ ප්රතිප්රවාහ උඳුනේ පුවරුව රත් කිරීමේ සහ සිසිලනය වීමේ වේගය මන්දගාමී වන තාක්, තහඩු නැමීම සහ යුධ පිටවීම විශාල වශයෙන් සිදුවිය හැකිය. අඩු කර ඇත.කෙසේ වෙතත්, පෑස්සුම් කෙටි පරිපථය වැනි වෙනත් අතුරු ආබාධ ඇති විය හැක.
2. ඉහළ Tg පත්රය භාවිතා කිරීම
Tg යනු වීදුරු සංක්රාන්ති උෂ්ණත්වය, එනම් ද්රව්ය වීදුරු තත්වයේ සිට රබර් තත්වයට වෙනස් වන උෂ්ණත්වයයි.ද්රව්යයේ Tg අගය අඩු වන තරමට, reflow උඳුනට ඇතුළු වූ පසු පුවරුව ඉක්මනින් මෘදු වීමට පටන් ගනී, සහ මෘදු රබර් තත්වයට පත් වීමට ගතවන කාලය එය ද දිගු වනු ඇත, සහ පුවරුවේ විරූපණය ඇත්ත වශයෙන්ම වඩාත් බරපතල වනු ඇත. .ඉහළ Tg පත්රයක් භාවිතා කිරීමෙන් ආතතියට සහ විරූපණයට ඔරොත්තු දීමේ හැකියාව වැඩි කළ හැකි නමුත් සාපේක්ෂ ද්රව්යයේ මිල ද ඉහළ ය.

3. පරිපථ පුවරුවේ ඝණකම වැඩි කරන්න බොහෝ ඉලෙක්ට්රොනික නිෂ්පාදන සඳහා සැහැල්ලු හා තුනී අරමුණ සාක්ෂාත් කර ගැනීම සඳහා, පුවරුවේ ඝණකම 1.0mm, 0.8mm, හෝ 0.6mm පවා ඉතිරි කර ඇත.එවැනි ඝනකම, reflow උදුනෙන් පසු විකෘති වීමෙන් පුවරුව තබා ගත යුතුය, එය ඇත්තෙන්ම දුෂ්කර ය.සැහැල්ලුබව සහ සිහින් වීම සඳහා අවශ්යතාවයක් නොමැති නම්, පුවරුවේ ඝණකම 1.6mm විය යුතු බව නිර්දේශ කරනු ලැබේ, එමඟින් පුවරුවේ නැමීමේ හා විකෘති වීමේ අවදානම බෙහෙවින් අඩු කළ හැකිය. 4. පරිපථ පුවරුවේ ප්රමාණය අඩු කර ප්රහේලිකා ගණන අඩු කරන්න බොහෝ ප්රතිප්රවාහ උදුන් පරිපථ පුවරුව ඉදිරියට ගෙන යාමට දාම භාවිතා කරන බැවින්, පරිපථ පුවරුවේ විශාලත්වය එහි බර, දත් සහ ප්රත්යාවර්ත උදුනේ ඇති විරූපණය නිසා සිදුවනු ඇත, එබැවින් පරිපථ පුවරුවේ දිගු පැත්ත තැබීමට උත්සාහ කරන්න. පුවරුවේ කෙළවර ලෙස.රිෆ්ලෝ උදුනේ දාමය මත, පරිපථ පුවරුවේ බර නිසා ඇතිවන අවපාතය සහ විරූපණය අඩු කළ හැකිය.පැනල් ගණන අඩු කිරීම ද මෙම හේතුව මත පදනම් වේ.එනම්, උදුන පසු කරන විට, හැකිතාක් දුරට උදුන දිශාව පසු කිරීමට පටු දාරය භාවිතා කිරීමට උත්සාහ කරන්න.මානසික අවපීඩනය විරූපණය වීමේ ප්රමාණය. 5. භාවිතා කරන ලද උදුන තැටි සවිකිරීම ඉහත ක්රම සාක්ෂාත් කර ගැනීමට අපහසු නම්, අවසාන ක්රමය වන්නේ විරූපණ ප්රමාණය අඩු කිරීම සඳහා reflow carrier/template භාවිතා කිරීමයි.රිෆ්ලෝ වාහකය/සැකිල්ලට තහඩුවේ නැමීම අඩු කළ හැක්කේ එය තාප ප්රසාරණය ද සීතල හැකිලීම ද යන්න බලාපොරොත්තු වන බැවිනි.තැටියට පරිපථ පුවරුව රඳවා තබාගෙන පරිපථ පුවරුවේ උෂ්ණත්වය Tg අගයට වඩා අඩු වන තෙක් බලා සිටිය හැකි අතර නැවත දැඩි වීමට පටන් ගන්නා අතර එය මුල් ප්රමාණය පවත්වා ගත හැකිය. තනි ස්ථර තට්ටුවට පරිපථ පුවරුවේ විරූපණය අඩු කළ නොහැකි නම්, ඉහළ සහ පහළ පැලට් සමඟ පරිපථ පුවරුව තද කිරීම සඳහා ආවරණයක් එකතු කළ යුතුය.මෙය reflow උදුන හරහා පරිපථ පුවරු විකෘති කිරීමේ ගැටලුව බෙහෙවින් අඩු කර ගත හැකිය.කෙසේ වෙතත්, මෙම උදුන තැටිය තරමක් මිල අධික වන අතර, තැටි තැබීමට සහ ප්රතිචක්රීකරණය කිරීමට ශ්රමික ශ්රමය අවශ්ය වේ. 6. උප පුවරුව භාවිතා කිරීමට V-Cut වෙනුවට Router භාවිතා කරන්න V-Cut මඟින් පරිපථ පුවරු අතර පුවරුවේ ව්යුහාත්මක ශක්තිය විනාශ කරන බැවින්, V-Cut උප පුවරුව භාවිතා නොකිරීමට හෝ V-කට් එකේ ගැඹුර අඩු කිරීමට උත්සාහ කරන්න.
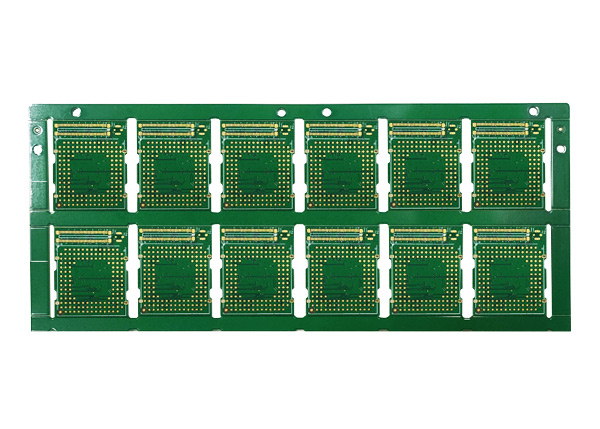
7. ඉංජිනේරු සැලසුම්කරණයේදී කරුණු තුනක් ක්රියාත්මක වේ: A. interlayer prepregs සැකැස්ම සමමිතික විය යුතුය, උදාහරණයක් ලෙස, හය-ස්ථර පුවරු සඳහා, 1~2 සහ 5~6 ස්ථර අතර ඝණකම සහ prepregs සංඛ්යාව සමාන විය යුතුය, එසේ නොමැති නම් එය ලැමිනේෂන් පසු විකෘති කිරීමට පහසු වේ. B. බහු-ස්ථර හර පුවරුව සහ ප්රෙප්රෙග් එකම සැපයුම්කරුගේ නිෂ්පාදන භාවිතා කළ යුතුය. C. පිටත ස්ථරයේ A සහ B පැත්තෙහි පරිපථ රටාවේ ප්රදේශය හැකි තරම් සමීප විය යුතුය.A පැත්ත විශාල තඹ මතුපිටක් නම් සහ B පැත්තේ ඇත්තේ රේඛා කිහිපයක් නම්, මේ ආකාරයේ මුද්රිත පුවරුවක් කැටයම් කිරීමෙන් පසු පහසුවෙන් විකෘති වේ.දෙපැත්තේ ඇති රේඛාවල ප්රදේශය බෙහෙවින් වෙනස් නම්, සමතුලිතතාවය සඳහා ඔබට තුනී පැත්තෙන් ස්වාධීන ජාල කිහිපයක් එකතු කළ හැකිය. 8. පූර්වයේ අක්ෂාංශ සහ දේශාංශ: Prepreg එක ලැමිෙන්ට් කිරීමෙන් පසු, warp සහ weft හැකිලීමේ අනුපාත වෙනස් වන අතර, හිස් කිරීම සහ ලැමිනේෂන් කිරීමේදී warp සහ weft දිශාවන් වෙන්කර හඳුනාගත යුතුය.එසේ නොමැති නම්, ලැමිනේෂන් කිරීමෙන් පසු නිමි පුවරුව විකෘති කිරීමට පහසු වන අතර, ෙබ්කිං පුවරුවට පීඩනය යෙදුවද එය නිවැරදි කිරීමට අපහසු වේ.බහු ස්ථර පුවරුවේ යුධ පිටුව සඳහා බොහෝ හේතු වනුයේ ලැමිනේෂන් කිරීමේදී පෙරනිමි සහ වෙෆ්ට් දිශාවන් වෙන්කර හඳුනා නොගැනීම සහ ඒවා අහඹු ලෙස ගොඩගැසීමයි. යුධ සහ වියන දිශාවන් වෙන්කර හඳුනා ගැනීමේ ක්රමය: රෝල් එකක පෙරළීමේ දිශාව යුධ දිශාව වන අතර පළල දිශාව වෙෆ්ට් දිශාව වේ;තඹ තීරු පුවරුව සඳහා, දිගු පැත්ත වියන දිශාව වන අතර කෙටි පැත්ත යුධ දිශාව වේ.ඔබට විශ්වාස නැත්නම්, කරුණාකර නිෂ්පාදකයා හෝ සැපයුම්කරු විමසන්න. 9. කැපීමට පෙර ෙබ්කිං පුවරුව: තඹ ආලේපිත ලැමිෙන්ට් (සෙල්සියස් අංශක 150, වේලාව පැය 8±2) කැපීමට පෙර පුවරුව පිළිස්සීමේ අරමුණ වන්නේ පුවරුවේ ඇති තෙතමනය ඉවත් කිරීම සහ ඒ සමඟම පුවරුවේ ඇති දුම්මල සම්පූර්ණයෙන්ම ඝන වීම සහ තවදුරටත් ඉවත් කිරීමයි. පුවරුවේ ඉතිරි ආතතිය, පුවරුව විකෘති වීම වැළැක්වීම සඳහා ප්රයෝජනවත් වේ.උදව් කරමින්.වර්තමානයේ, බොහෝ ද්විත්ව ඒක පාර්ශවීය සහ බහු ස්ථර පුවරු තවමත් හිස් කිරීමට පෙර හෝ පසුව පිළිස්සීමේ පියවරට අනුගත වේ.කෙසේ වෙතත්, සමහර තහඩු කර්මාන්තශාලා සඳහා ව්යතිරේක පවතී.විවිධ PCB කර්මාන්තශාලා වල වර්තමාන PCB වියලීමේ කාල රෙගුලාසි ද නොගැලපේ, පැය 4 සිට 10 දක්වා පරාසයක පවතී.නිෂ්පාදනය කරන ලද මුද්රිත පුවරුවේ ශ්රේණිය සහ warpage සඳහා පාරිභෝගිකයාගේ අවශ්යතා අනුව තීරණය කිරීම රෙකමදාරු කරනු ලැබේ.ජිජැක් එකකට කැපීමෙන් පසු පුළුස්සන්න හෝ සම්පූර්ණ බ්ලොක් පුළුස්සා දැමීමෙන් පසු හිස් කරන්න.ක්රම දෙකම ශක්ය වේ.කැපීමෙන් පසු පුවරුව පිළිස්සීම නිර්දේශ කරනු ලැබේ.ඇතුල් තට්ටුවේ පුවරුව ද පුළුස්සා දැමිය යුතුය ... 10. ලැමිනේෂන් කිරීමෙන් පසු ආතතියට අමතරව: බහු ස්ථර පුවරුව උණුසුම්ව තද කර සීතලෙන් තද කළ පසු, එය පිටතට ගෙන, කපා හෝ ඇඹරීමට, පසුව සෙල්සියස් අංශක 150 ක උඳුනක පැය 4 ක් සමතලා කර ඇති අතර එමඟින් පුවරුවේ ආතතිය ඇති වේ. ක්රමයෙන් නිදහස් වන අතර දුම්මල සම්පූර්ණයෙන්ම සුව වේ.මෙම පියවර මඟ හැරිය නොහැක.
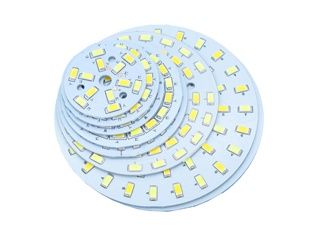
11. විද්යුත් ආලේපනයේදී තුනී තහඩුව කෙළින් කළ යුතුය: 0.4 ~ 0.6mm අල්ට්රා තුනී බහු ස්ථර පුවරුව මතුපිට විද්යුත් ආලේපනය සහ රටා විද්යුත් ආලේපනය සඳහා භාවිතා කරන විට, විශේෂ කලම්ප රෝලර් සෑදිය යුතුය.තුනී තහඩුව ස්වයංක්රීය විද්යුත් ආලේපන රේඛාව මත පියාසර බස් රථයේ තද කළ පසු, සම්පූර්ණ පියාසර බස් රථය තද කිරීමට රවුම් පොල්ලක් භාවිතා කරයි.තහඩු දැමීමෙන් පසු තහඩු විකෘති නොවන පරිදි රෝලර් මත ඇති සියලුම තහඩු කෙළින් කිරීම සඳහා රෝලර් එකට සවි කර ඇත.මෙම මිනුමකින් තොරව, මයික්රෝන 20 සිට 30 දක්වා තඹ තට්ටුවක් විද්යුත් ආලේපනය කිරීමෙන් පසුව, පත්රය නැමෙන අතර එය පිළියමක් කිරීමට අපහසු වේ. 12. උණුසුම් වාතය මට්ටම් කිරීමෙන් පසු පුවරුව සිසිල් කිරීම: මුද්රිත පුවරුව උණුසුම් වාතය මගින් සමතලා කරන විට, පෑස්සුම් ස්නානයේ (සෙල්සියස් අංශක 250 ක් පමණ) ඉහළ උෂ්ණත්වයකින් එය බලපායි.පිටතට ගැනීමෙන් පසු, එය ස්වභාවික සිසිලනය සඳහා පැතලි කිරිගරුඬ හෝ වානේ තහඩු මත තැබිය යුතුය, පසුව පිරිසිදු කිරීම සඳහා පශ්චාත් සැකසුම් යන්ත්රයකට යැවිය යුතුය.පුවරුවේ යුධ පිටවීම වැළැක්වීම සඳහා මෙය හොඳයි.සමහර කර්මාන්තශාලා වල, ඊයම්-ටින් මතුපිට දීප්තිය වැඩි දියුණු කිරීම සඳහා, උණුසුම් වාතය සමතලා කළ වහාම පුවරු සීතල වතුරට දමනු ලැබේ, පසුව පසු සැකසුම් සඳහා තත්පර කිහිපයකින් පසුව පිටතට ගෙන යයි.මෙම ආකාරයේ උණුසුම් හා සීතල බලපෑම් සමහර පුවරු වර්ග මත විකෘති වීමට හේතු විය හැක.ඇඹරුණු, ස්ථර හෝ බිබිලි.මීට අමතරව, සිසිලනය සඳහා උපකරණ මත වායු පාවෙන ඇඳක් ස්ථාපනය කළ හැකිය. 13. විකෘති පුවරුවට ප්රතිකාර කිරීම: හොඳින් කළමනාකරණය කරන ලද කර්මාන්ත ශාලාවක, මුද්රිත පුවරුව 100% සමතලා බව අවසාන පරීක්ෂාවේදී පරීක්ෂා කරනු ලැබේ.සියලුම නුසුදුසු පුවරු අහුලා, උඳුන තුල තබා, සෙල්සියස් අංශක 150 ට අධික පීඩනය යටතේ පැය 3-6 ක් පුළුස්සනු ලබන අතර, අධික පීඩනය යටතේ ස්වභාවිකව සිසිල් කරනු ලැබේ.ඉන්පසු පුවරුව පිටතට ගැනීමට ඇති පීඩනය සමනය කර සමතලා බව පරීක්ෂා කරන්න, එවිට පුවරුවේ කොටසක් ඉතිරි කර ගත හැකි අතර, සමහර පුවරු මට්ටම් කිරීමට පෙර දෙතුන් වතාවක් පිළිස්සීම සහ තද කළ යුතුය.ඉහත සඳහන් කළ ප්රති-වර්ණ ක්රියාවලි ක්රියාමාර්ග ක්රියාත්මක නොකළහොත්, සමහර පුවරු නිෂ්ඵල වන අතර ඒවා ඉවත් කළ හැකිය.