SMT( プリント基板アセンブリ 、 PCBA ) 表面実装技術とも呼ばれます。製造プロセス中、はんだペーストは加熱環境で加熱され、溶融するため、PCB パッドははんだペースト合金を介して表面実装部品と確実に結合されます。このプロセスをリフローはんだ付けと呼びます。ほとんどの回路基板は、リフロー(リフローはんだ付け)を行うと基板が曲がったり、反ったりしやすくなります。ひどい場合には、空はんだや墓石などの部品が発生することもあります。 自動組立ラインでは、回路基板工場の PCB が平坦でない場合、位置決めが不正確になり、部品を基板の穴や表面実装パッドに挿入できなくなり、さらには自動挿入機が損傷する可能性があります。部品が実装された基板が溶接後に曲がってしまい、部品の足をきれいに切断するのが困難です。基板はシャーシや機械内部のソケットに取り付けることができないため、基板の反りは組立工場にとっても非常に迷惑です。現在、プリント基板は表面実装、チップ実装の時代を迎えており、組立工場における基板の反りに対する要求はますます厳しくなっています。
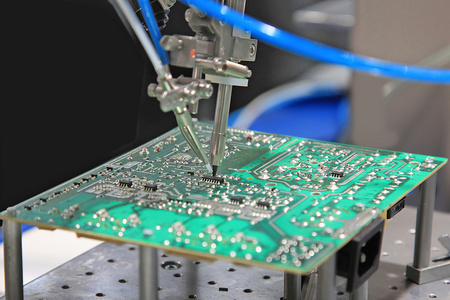
米国の IPC-6012 (1996 年版)「仕様および性能仕様」によると、 リジッドプリント基板 「」では、表面実装プリント基板の反り・歪みの許容値は0.75%、その他の基板は1.5%となっており、IPC-RB-276(1992年版)と比較して、表面実装プリント基板の要求条件が向上しました。現在、各種電子組立工場で許容される反りは、両面、多層を問わず、1.6mm厚で通常0.70~0.75%となっております。
多くの SMT および BGA ボードの要件は 0.5% です。一部の電子工場では反りの基準を0.3%まで引き上げるように求めている。反り試験方法はGB4677.5-84またはIPC-TM-650.2.4.22Bに準拠します。検証済みのプラットフォームにプリント基板を置き、最も反りの度合いが大きい箇所にテストピンを挿入し、テストピンの直径をプリント基板の湾曲端の長さで割って反りを算出します。プリント基板。曲がりはなくなりました。

そのため、PCB の製造プロセスでは、 板が曲がったり反ったりする原因は何ですか?
板の曲がりや反りの原因はそれぞれ異なりますが、いずれも板材が耐えられる応力を超える応力が板に加わっていることが原因であると考えられます。基板に不均一な応力が加わったり、基板の各箇所の耐応力が不均一になったりすると、基板の曲がりや基板の反りが発生します。プレートの曲がり、プレートの反りの主な原因を以下に4つまとめます。
1. 回路基板上の銅の表面領域が不均一であると、基板の曲がりや反りが悪化します。
一般に、回路基板上の銅箔の広い領域は、接地の目的で設計されます。場合によっては、Vcc 層上に広い領域の銅箔も設計されることがあります。このような大面積の銅箔を同一基板上に均一に配置できない場合、熱の吸収や放熱が不均一になるという問題が発生します。当然、基板も熱により伸縮します。膨張と収縮を同時に行うことができない場合、異なる応力と変形が発生します。このとき、基板温度がTgの上限値に達すると基板は軟化し始め、永久変形が発生します。
2. 基板自体の重みにより基板が凹んだり変形したりすることがあります。
一般に、リフロー炉ではチェーンを使用して回路基板をリフロー炉内で前方に駆動します。つまり、基板の両側を支点として基板全体を支えます。ボード上に重いパーツがあったり、ボードのサイズが大きすぎると、シードの量により中央がくぼみ、プレートが曲がってしまうことがあります。
3. V カットの深さと接続ストリップはジグソーの変形に影響します。
基本的に基板の構造を壊す元凶はVカットです。Vカットはオリジナルの大きなシートにV字型の溝を切るため、変形しやすいのです。
4. 回路基板上の各層の接続ポイント(ビア)により、基板の伸縮が制限されます。
現在の回路基板は多層基板が多く、層間にはリベット状の接続点(ビア)が存在します。接続点はスルーホール、ブラインドホール、埋め込みホールに分けられます。接続ポイントがある場合、ボードは制限されます。膨張と収縮の影響は間接的にプレートの曲がりやプレートの反りを引き起こします。
では、製造工程中の基板の反りの問題をよりよく防ぐにはどうすればよいでしょうか? ここでは効果的な方法をいくつか紹介しますので、お役に立てれば幸いです。
1. 基板の応力に対する温度の影響を軽減します。
基板応力の主な原因は「温度」であるため、リフロー炉の温度を下げたり、リフロー炉内での基板の加熱・冷却速度を遅くしたりすると、プレートの曲がりや反りが大幅に発生する可能性があります。削減。ただし、はんだショートなどの他の副作用が発生する可能性があります。
2.高Tgシートの使用
Tg はガラス転移温度、つまり材料がガラス状態からゴム状態に変化する温度です。材料のTg値が低いほど、リフロー炉に入ってから基板が軟化し始めるのが早くなり、柔らかいゴム状態になるまでの時間も長くなり、当然基板の変形も大きくなります。 。より高い Tg シートを使用すると、応力や変形に対する耐性が向上しますが、相対的な材料の価格も高くなります。

3. 回路基板の厚さを増やす 多くの電子製品では軽量化、薄型化という目的を達成するために、基板の厚さは1.0mm、0.8mm、さらには0.6mmまで残されています。このような厚さは、リフロー炉後の基板の変形を防ぐ必要がありますが、これは非常に困難です。軽さと薄さの要件がない場合、ボードの厚さは 1.6 mm にすることをお勧めします。これにより、ボードの曲がりや変形のリスクが大幅に軽減されます。 4. 回路基板のサイズを縮小し、パズルの数を削減します。 多くのリフロー炉はチェーンを使用して基板を前方に駆動するため、リフロー炉内での自重や凹み、変形により基板サイズが大きくなりますので、基板の長辺を長辺側に配置するようにしてください。ボードの端として。リフロー炉のチェーン上で、回路基板の重量による凹みや変形を軽減できます。パネル枚数の削減もこの理由によるものです。つまり、炉を通過するときは、狭いエッジを使用して、できるだけ炉の方向を通過するようにしてください。くぼみの変形量。 5. 使用済み炉トレイ治具 上記の方法を達成するのが難しい場合、最後にリフローキャリア/テンプレートを使用して変形量を減らす方法があります。リフローキャリア/テンプレートがプレートのたわみを軽減できるのは、熱膨張や冷間収縮によるプレートのたわみを軽減できるからです。トレイは回路基板を保持し、回路基板の温度が Tg 値より低くなって再び硬化し始めるまで待つことができ、元のサイズを維持することもできます。 単層パレットで回路基板の変形を軽減できない場合は、上下のパレットで回路基板をクランプするためのカバーを追加する必要があります。これにより、リフロー炉による回路基板の変形の問題を大幅に軽減できます。しかし、この炉用トレイは非常に高価であり、トレイを配置してリサイクルするには手作業が必要です。 6. サブボードを使用するには、V-Cut の代わりに Router を使用します。 Vカットは基板間の基板の構造強度を破壊しますので、Vカットサブ基板を使用しないか、Vカットの深さを浅くしてください。
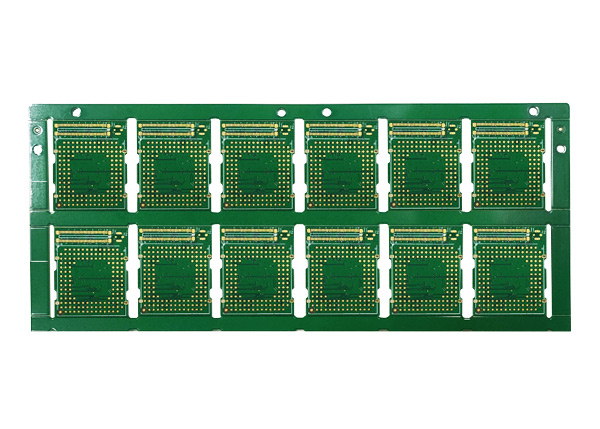
7. エンジニアリング設計では次の 3 つのポイントが貫かれます。 A. 中間層プリプレグの配置は対称である必要があります。たとえば、6 層基板の場合、1 ~ 2 層と 5 ~ 6 層の厚さとプリプレグの枚数が同じである必要があります。そうしないと、積層後に反りやすくなります。 B. 多層コア基板とプリプレグは同じサプライヤーの製品を使用する必要があります。 C. 外層の A 面と B 面の回路パターンの面積はできるだけ近くなければなりません。A 面が大きな銅表面で、B 面に数本の線しかない場合、この種のプリント基板はエッチング後に反りやすくなります。両側の線の面積が違いすぎる場合は、細い側に独立したグリッドを追加してバランスをとることができます。 8. プリプレグの緯度と経度: プリプレグを積層した後、経糸と緯糸の収縮率が異なるため、打ち抜きおよび積層時に経糸と緯糸の方向を区別する必要があります。そうしないと、積層後に完成した基板が反りやすくなり、天板に圧力を加えても修正することが困難になります。多層基板の反りの原因としては、積層時にプリプレグの縦方向と横方向の区別が無く、ランダムに積層されることが多くの原因となります。 経糸方向と緯糸方向を区別する方法。プリプレグをロール状に巻き取る方向を経糸方向、幅方向を緯糸方向とする。銅箔板は長辺が緯方向、短辺が経方向になります。ご不明な点がございましたら、メーカーまたはサプライヤーにお問い合わせください。 9. カットする前のベーキングボード: 銅張積層板を切断する前に基板をベーキング(150℃、時間8±2時間)するのは、基板内の水分を除去すると同時に基板内の樹脂を完全に固化させ、さらに汚れを除去するためです。基板の残留応力を軽減し、基板の反りを防止します。お手伝い。現在、多くの両面基板や多層基板では、ブランキングの前後にベーキング工程が行われています。ただし、一部の製版工場では例外があります。現在のさまざまな PCB 工場の PCB 乾燥時間規制も 4 ~ 10 時間とばらつきがあります。製作するプリント基板のグレードやお客様の反りに対する要求に応じて決定することをお勧めします。ジグソーにカットしてから焼くか、ブロック全体が焼き上がってからブランキングしてください。どちらの方法も実行可能です。カット後はベーキング処理を行うことをお勧めします。内層基板も焼かないといけないのですが・・・。 10. ラミネート後の応力に加えて: 多層基板をホットプレスおよびコールドプレスした後、取り出し、切断またはフライス加工でバリを取り除き、平らに 150 ℃のオーブンに 4 時間入れて基板内の応力を緩和します。徐々に放出され、樹脂は完全に硬化します。このステップは省略できません。
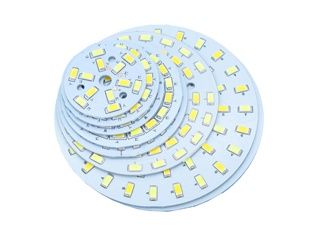
11. 電気めっき中に薄いプレートを真っ直ぐにする必要があります。 0.4~0.6mmの極薄多層基板を表面電気めっきやパターン電気めっきに使用する場合は、専用のクランプローラーを製作する必要があります。薄板が自動電気めっきライン上のフライバスにクランプされた後、丸棒を使用してフライバス全体をクランプします。メッキ後の板が変形しないように、ローラーを張ってローラー上のすべての板を真っすぐに整えます。この措置を講じないと、20 ~ 30 ミクロンの銅層を電気めっきした後、シートが曲がってしまい、それを修正するのが困難になります。 12. 熱風レベリング後の基板の冷却: 熱風でプリント基板を平らにすると、はんだ槽の高温(約250℃)の影響を受けます。取り出した後は、平らな大理石や鋼板の上に置いて自然冷却し、後処理機に送って洗浄します。基板の反り防止に効果があります。工場によっては、鉛錫表面の光沢を高めるために、熱風をならした直後に基板を冷水に入れ、数秒後に取り出して後処理を行う場合もあります。このような高温と低温の衝撃により、特定の種類のボードに反りが生じる場合があります。ねじれたり、層になったり、水膨れができたりします。さらに、冷却用に空気浮遊ベッドを装置に取り付けることもできます。 13. 反った基板の処理: 管理の行き届いた工場では、プリント基板の最終検査時に100%平坦度がチェックされます。不適格なボードはすべて選別され、オーブンに入れられ、高圧下で 150 ℃で 3 ~ 6 時間焼き、高圧下で自然冷却されます。次に、圧力を緩めてボードを取り出し、平坦度を確認します。これにより、ボードの一部が保存されます。ボードによっては、水平になるまでに 2 ~ 3 回ベーキングしてプレスする必要があります。上記の反り防止プロセス対策を実施しない場合、一部の基板は役に立たず、廃棄するしかありません。