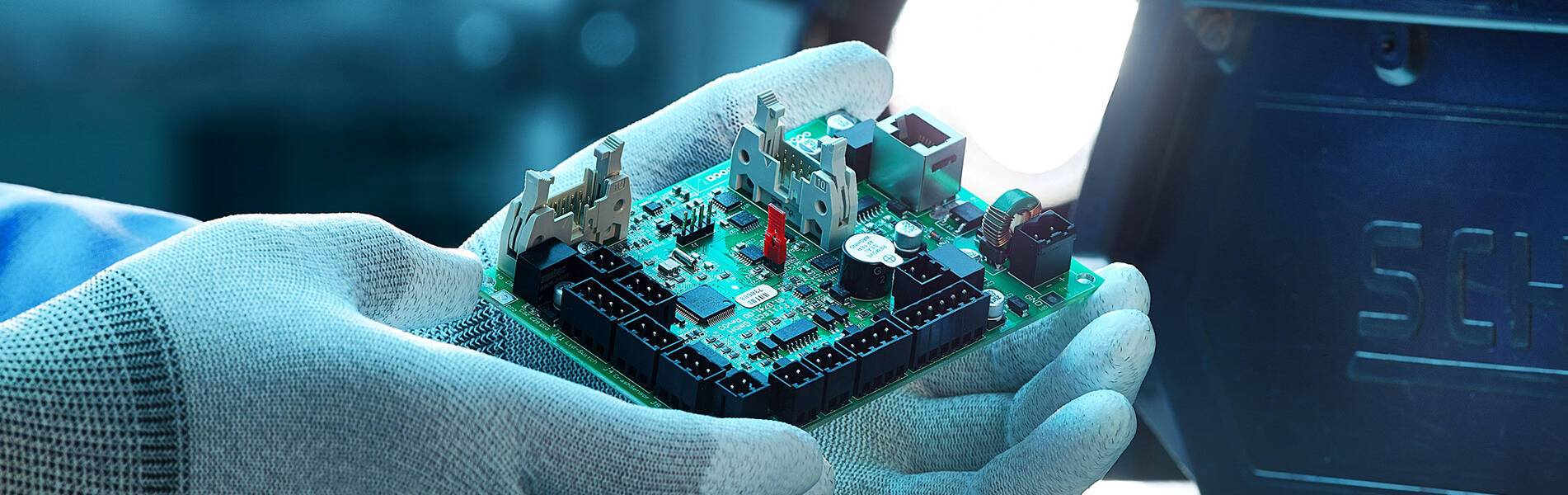
Introduction to plasma processing on PCB boards
With the advent of the digital information age, the requirements of high-frequency communication, high-speed transmission, and high-confidentiality of communications are becoming higher and higher. As an indispensable supporting product for the electronic information technology industry, PCB requires the substrate to meet the performance of low dielectric constant, low media loss factor, high-temperature resistance, etc., and to meet these performance needs to use special high-frequency substrates, of which the more commonly used is Teflon (PTFE) materials. However, in the PCB processing process, due to the poor surface wetting performance of Teflon material, surface wetting by plasma treatment is required before the hole metallization, to ensure the smooth progress of the hole metalization process.
What is Plasma?
Plasma is a form of matter consisting mainly of free electrons and charged ions, widely found in the universe, often considered to be the fourth state of matter, known as plasma, or "Ultra gaseous state", also known as "plasma". Plasma has high conductivity and is highly coupled with electromagnetic fields.
Mechanism
The application of energy (e.g. electrical energy) in a gas molecule in a vacuum chamber is caused by the collision of accelerated electrons, inflaming the outermost electrons of molecules and atoms, and generating ions, or highly reactive free radicals. Thus the resulting ions, free radicals are continuously collided and accelerated by electric field force, so that it collides with the surface of the material, and destroys the molecular bonds within the range of several microns, induces the reduction of a certain thickness, generates bumpy surfaces, and at the same time forms the physical and chemical changes of the surface such as the function group of gas composition, improves copper-plated bonding force, decontamination and other effects.
Oxygen, nitrogen, and Teflon gas are commonly used in the above plasma.
Plasma processing used in the PCB field
A contrast chart of the effects after processing
1. Hydrophilic improvement experiment
2. Copper-plated SEM in the RF-35 sheet holes before and after plasma treatment
3. Copper deposition on the surface of the PTFE Base board before and after plasma modification
4. The Solder mask condition of the surface of the PTFE base board before and after plasma modification
Description of plasma action
1, Activated treatment of Teflon material
But all engineers who have been engaged in the metallization of polytetrafluoroethylene material holes have this experience: the use of ordinary FR-4 multi-layer printed circuit board hole metalization processing method, is not successful PTFE hole metalization. Among them, pre-activation treatment of PTFE before the chemical copper deposition is a great difficulty and a key step. In the activation treatment of PTFE material before chemical copper deposition, many methods can be used, but on the whole, it can guarantee the quality of products, suitable for mass production purposes are the following two:
a) Chemical processing method: metal sodium and radon, the reaction in non-water solvents such as tetrahydrofuran or glycol dimethyl ether solution, the formation of a nio-sodium complex, the sodium treatment solution, can make the surface atoms of Teflon in the hole are impregnated, to achieve the purpose of wetting the hole wall. This is a typical method, good effect, stable quality, is widely used.
b) Plasma treatment method: this process is simple to operate, stable and reliable processing quality, suitable for mass production, the use of plasma drying process production. The sodium-crucible treatment solution prepared by the chemical treatment method is difficult to synthesize, high toxicity, short shelf life, needs to be formulated according to the production situation, high safety requirements. Therefore, at present, the activation treatment of PTFE surface, more plasma treatment method, easy to operate, and greatly reduce the treatment of wastewater.
2, Hole wall cavitation/hole wall resin drilling removal
For FR-4 multi-layer printed circuit board processing, its CNC drilling after the hole wall resin drilling and other substances removal, usually using concentrated sulfuric acid treatment, chromic acid treatment, alkaline potassium permanganate treatment, and plasma treatment. However, in the flexible printed circuit board and rigid-flexible printed circuit board to remove drilling dirt treatment, due to the differences in material characteristics, if the use of the above chemical treatment methods, the effect is not ideal, and the use of plasma to drill dirt and concave removal, you can get a better hole wall roughness, conducive to the metallic plating of the hole, but also has a "three-dimensional" concave connection characteristics.
3, The removal of a carbide
Plasma treatment method, not only for a variety of sheet drilling pollution treatment effect is obvious, but also for composite resin materials and micropores drilling pollution treatment, but also show its superiority. In addition, due to the increasing production demand for layered multi-layer printed circuit boards with high interconnect density, many drilling blind holes are manufactured using laser technology, which is a by-product of laser drilling blind hole applications - carbon, which needs to be removed before the hole metallization process. At this time, plasma treatment technology, without hesitation to assume the responsibility of removing carbon.
4, Internal pre-processing
Due to the increasing production demand of various printed circuit boards, the corresponding processing technology requirements are also higher and higher. The internal pretreatment of flexible printed circuit board and rigid flexible printed circuit board can increase surface roughness and activation degree, increase the binding force between inner layer, and also have great significance to improve the yield of production.
The advantages and disadvantages of plasma processing
Plasma processing is a convenient, efficient and high-quality method for decontamination and back etching of printed circuit boards. Plasma treatment is particularly suitable for Teflon (PTFE) materials because they are less chemically active and plasma treatment activates activity. Through the high-frequency generator (typical 40KHZ), plasma technology is established by using the energy of the electric field to separate the processing gas under vacuum conditions. These stimulate unstable separation gases that modify and bombard the surface. Treatment processes such as fine UV cleaning, activation, consumption and crosslinking, and plasma polymerization are the role of plasma surface treatment. Plasma processing process is before drilling copper, mainly the treatment of holes, the general plasma processing process is: drilling - plasma treatment - copper. Plasma treatment can solve the problems of hole hole, residue residue, poor electrical binding of inner copper layer and inadequate corrosion. Specifically, plasma treatment can effectively remove resin residues from the drilling process, also known as drilling contamination. It hinders the connection of the hole copper to the inner copper layer during metalization. In order to improve the binding force between plating and resin, fiberglass and copper, these slags must be removed clean. Therefore, plasma degluing and corrosion treatment ensure an electrical connection after copper deposition.
Plasma machines generally consist of processing chambers that are held in a vacuum and are located between two electrode plates, which are connected to an RF generator to form a large number of plasmas in the processing chamber. In the processing chamber between the two electrode plates, the equidistant setting has several pairs of opposite card slots to form a shelter space for multi-gram can accommodate plasma processing circuit boards. In the existing plasma processing process of PCB board, when the PCB substrate is placed in the plasma machine for plasma processing, a PCB substrate is generally placed correspondingly between a relative card slot of the plasma processing chamber (i.e., a compartment containing the plasma processing circuit board), the plasma is used to plasma to plasma treatment of the hole on the PCB substrate to improve the surface moisture of the hole.
Plasma machine processing cavity space is small, therefore, generally between the two electrode plate processing chamber is set up with four pairs of opposite card plate grooves, that is, the formation of four blocks can accommodate plasma processing circuit board shelter space. In general, the size of each grid of shelter space is 900mm (long) x 600mm (height) x 10mm (wide, i.e. the thickness of the board), according to the existing PCB board plasma processing process, each time The plasma processing board has a capacity of approximately 2 flat (900mm x 600mm x 4), while each plasma processing cycle time is 1.5 hours, thus giving a one-day capacity of about 35 square meters. It can be seen that the plasma processing capacity of PCB board is not high by using the plasma processing process of the existing PCB board.
Summary
Plasma treatment is mainly used in high-frequency plate, HDI, hard and soft combination, especially suitable for Teflon (PTFE) materials. Low production capacity, high cost is also its disadvantage, but plasma treatment advantages are also obvious, compared to other surface treatment methods, it in the treatment of Teflon activation, improve its hydrophilicity, to ensure that the metallization of holes, laser hole treatment, removal of precision line residual dry film, roughing, pre-reinforcement, welding and silkscreen character pretreatment, its advantages are irreplaceable, and also have clean, environmentally friendly characteristics.
New Blog
Copyright © 2025 ABIS CIRCUITS CO., LTD. All Rights Reserved. Power by
IPv6 network supported