ගෝලීය විද්යුත් ආලේපන PCB කර්මාන්තයේ නිමැවුම් අගය ඉලෙක්ට්රොනික සංරචක කර්මාන්තයේ සම්පූර්ණ නිමැවුම් අගය තුළ වේගයෙන් වර්ධනය වී ඇත.එය ඉලෙක්ට්රොනික උපාංග අනුකොටස් කර්මාන්තයේ විශාලතම ප්රතිශතයක් ඇති කර්මාන්තය වන අතර අද්විතීය ස්ථානයක් හිමිකර ගනී.විද්යුත් ආලේපන PCB හි වාර්ෂික නිමැවුම් අගය ඇමරිකානු ඩොලර් බිලියන 60 කි.ඉලෙක්ට්රොනික නිෂ්පාදනවල පරිමාව වඩ වඩාත් සිහින් සහ කෙටි වෙමින් පවතින අතර, අන්ධ හරහා හරහා සෘජුව ඇමිණීම අධි-ඝනත්ව අන්තර් සම්බන්ධතාවක් ලබා ගැනීමේ සැලසුම් ක්රමයකි.හොඳ ස්ටැකිං සිදුරක් කිරීමට, පළමුවෙන්ම, සිදුරු පතුලේ සමතලා කිරීම හොඳින් සිදු කළ යුතුය.සාමාන්ය පැතලි සිදුරු මතුපිටක් සෑදීමට ක්රම කිහිපයක් ඇති අතර විද්යුත් ආලේපන සිදුරු පිරවීමේ ක්රියාවලිය නියෝජිත එකකි. අමතර ක්රියාවලි සංවර්ධනය සඳහා අවශ්යතාවය අඩු කිරීමට අමතරව, විද්යුත් ආලේපන සහ සිදුරු පිරවීමේ ක්රියාවලිය වත්මන් ක්රියාවලි උපකරණ සමඟ අනුකූල වන අතර එය හොඳ විශ්වසනීයත්වයක් ලබා ගැනීමට උපකාරී වේ. විද්යුත් ආලේපන සිදුරු පිරවීමට පහත වාසි ඇත: (1) Stacked සහ Via.on.Pad සැලසුම් කිරීම ප්රයෝජනවත් වේ ( HDI පරිපථ පුවරුව ); (2) විදුලි කාර්ය සාධනය වැඩි දියුණු කිරීම සහ උපකාර කිරීම අධි-සංඛ්යාත නිර්මාණය ; (3) තාපය විසුරුවා හැරීමට උපකාරී වේ; (4) ප්ලග් කුහරය සහ විදුලි අන්තර් සම්බන්ධතාව එක් පියවරකින් සම්පූර්ණ කර ඇත; (5) සන්නායක මැලියම් වලට වඩා ඉහළ විශ්වසනීයත්වයක් සහ වඩා හොඳ සන්නායකතාවයක් ඇති විද්යුත් තැටි තඹ වලින් අන්ධ සිදුරු පුරවා ඇත.

භෞතික බලපෑම් පරාමිතීන් අධ්යයනය කළ යුතු භෞතික පරාමිතීන් වනුයේ: ඇනෝඩ වර්ගය, කැතෝඩ-ඇනෝඩ පරතරය, වත්මන් ඝනත්වය, උද්ඝෝෂණය, උෂ්ණත්වය, සෘජුකාරක සහ තරංග ආකෘතිය, ආදිය. (1) ඇනෝඩ වර්ගය.ඇනෝඩ වර්ග සම්බන්ධයෙන් ගත් කල, එය ද්රාව්ය ඇනෝඩ සහ දිය නොවන ඇනෝඩ වලට වඩා වැඩි දෙයක් නොවේ.ද්රාව්ය ඇනෝඩ සාමාන්යයෙන් පොස්පරස් අඩංගු තඹ බෝල වන අතර ඒවා ඇනෝඩ ස්ලයිම් නිපදවීමට පහසුය, ප්ලේටින් ද්රාවණය දූෂණය කරයි, සහ ප්ලේටින් ද්රාවණයේ ක්රියාකාරිත්වයට බලපායි.නිෂ්ක්රීය ඇනෝඩ ලෙසද හැඳින්වෙන ද්රාව්ය නොවන ඇනෝඩ සාමාන්යයෙන් සමන්විත වන්නේ ටැන්ටලම් සහ සර්කෝනියම් මිශ්ර ඔක්සයිඩ සහිත ටයිටේනියම් දැලකිනි.දිය නොවන ඇනෝඩය, හොඳ ස්ථායීතාවයක්, ඇනෝඩ නඩත්තු කිරීමක් නැත, ඇනෝඩ රොන්මඩ නැත, ස්පන්දන හෝ DC විද්යුත් ආලේපනය සඳහා සුදුසු ය;කෙසේ වෙතත්, ආකලන පරිභෝජනය විශාල වේ. (2) කැතෝඩය සහ ඇනෝඩය අතර දුර.පිරවුම් ක්රියාවලිය හරහා විද්යුත් ආලේපනයේදී කැතෝඩය සහ ඇනෝඩය අතර පරතරය නිර්මාණය ඉතා වැදගත් වන අතර විවිධ වර්ගයේ උපකරණ සැලසුම් කිරීමද වෙනස් වේ.කෙසේ වෙතත්, එය කෙසේ නිර්මාණය කළද, එය ෆාරාගේ පළමු නීතිය උල්ලංඝනය නොකළ යුතු බව පෙන්වා දිය යුතුය. (3) ඇවිස්සීම.යාන්ත්රික සෙලවීම, විද්යුත් කම්පනය, වායු කම්පනය, වාතය කලවම් කිරීම, එඩක්ටර් යනාදී බොහෝ වර්ග තිබේ. විද්යුත් ආලේපනය සහ පිරවීම සඳහා, සාම්ප්රදායික තඹ සිලින්ඩරයේ වින්යාසය මත පදනම්ව ජෙට් නිර්මාණය වැඩි කිරීමට සාමාන්යයෙන් කැමැත්තක් දක්වයි.කෙසේ වෙතත්, එය පහළ ජෙට් හෝ පැති ජෙට් වේවා, සිලින්ඩරයේ ජෙට් නළය සහ වාතය ඇවිස්සීමේ නළය සකස් කරන්නේ කෙසේද;පැයකට ජෙට් ප්රවාහය කොපමණද;ජෙට් ටියුබ් සහ කැතෝඩය අතර දුර කොපමණද;පැති ජෙට් යානය භාවිතා කරන්නේ නම්, ජෙට් යානය ඇනෝඩයේ ඉදිරිපස හෝ පිටුපස ඇත;පහළ ජෙට් භාවිතා කරන්නේ නම්, එය අසමාන ඇවිස්සීමක් ඇති කරයිද, සහ ප්ලේටින් ද්රාවණය දුර්වල ලෙස ඉහළට සහ පහළට ඇවිස්සී ඇත;පරීක්ෂණ ගොඩක් කරන්න. මීට අමතරව, වඩාත් පරමාදර්ශී මාර්ගය වන්නේ ප්රවාහය නිරීක්ෂණය කිරීමේ අරමුණ සාක්ෂාත් කර ගැනීම සඳහා, එක් එක් ජෙට් නලයක් ප්රවාහ මීටරයට සම්බන්ධ කිරීමයි.විශාල ජෙට් ප්රවාහය හේතුවෙන් ද්රාවණය තාපයට ගොදුරු වේ, එබැවින් උෂ්ණත්ව පාලනය ද වැදගත් වේ. (4) වත්මන් ඝනත්වය සහ උෂ්ණත්වය.අඩු ධාරා ඝනත්වය සහ අඩු උෂ්ණත්වය මගින් මතුපිට තඹ තැන්පත් වීමේ වේගය අඩු කළ හැකි අතර, ප්රමාණවත් Cu2 සහ සිදුර තුළට දීප්තිය ලබා දෙයි.මෙම තත්වයන් යටතේ, සිදුරු පිරවීමේ හැකියාව වැඩි දියුණු කර ඇත, නමුත් තහඩු කිරීමේ කාර්යක්ෂමතාව ද අඩු වේ. (5) සෘජුකාරකය.සෘජුකාරකය විද්යුත් ආලේපන ක්රියාවලියේ වැදගත් සම්බන්ධකයකි.වර්තමානයේ, විද්යුත් ආලේපනය සහ පිරවීම පිළිබඳ පර්යේෂණ බොහෝ දුරට සම්පූර්ණ පුවරු විද්යුත් ආලේපනයට සීමා වී ඇත.රටාව විද්යුත් ආලේපනය සහ පිරවීම සලකා බැලුවහොත්, කැතෝඩ ප්රදේශය ඉතා කුඩා වනු ඇත.මෙම අවස්ථාවේදී, සෘජුකාරකයේ ප්රතිදාන නිරවද්යතාව සඳහා ඉහළ අවශ්යතා ඉදිරිපත් කරනු ලැබේ. සෘජුකාරකයේ ප්රතිදාන නිරවද්යතාව තෝරාගැනීම නිෂ්පාදනයේ රේඛාව සහ හරහා කුහරයේ ප්රමාණය අනුව තීරණය කළ යුතුය.සිහින් රේඛා සහ කුඩා සිදුරු, සෘජුකාරකයේ නිරවද්යතා අවශ්යතා වැඩි විය යුතුය.සාමාන්යයෙන්, 5% ක් ඇතුළත නිමැවුම් නිරවද්යතාවයක් සහිත සෘජුකාරකයක් තෝරා ගැනීම සුදුසුය.ඉතා නිවැරදි සෘජුකාරකයක් තෝරා ගැනීමෙන් උපකරණවල ආයෝජනය වැඩි වේ.සෘජුකාරකයේ ප්රතිදාන කේබලය රැහැන්ගත කිරීමේදී, ප්රථමයෙන් ප්ලේටින් ටැංකියේ අද්දර සෘජුකාරකය තබන්න, එමඟින් ප්රතිදාන කේබලයේ දිග අඩු කර ස්පන්දන ධාරාවේ නැගීමේ කාලය අඩු කළ හැකිය.සෘජුකාරක ප්රතිදාන කේබල් පිරිවිතර තෝරාගැනීම උපරිම ප්රතිදාන ධාරාවෙන් 80% දී 0.6V තුළ ප්රතිදාන කේබලයේ රේඛීය වෝල්ටීයතා පහත වැටීම සපුරාලිය යුතුය.සාමාන්යයෙන්, අවශ්ය කේබල් හරස්කඩ ප්රදේශය 2.5A/mm වත්මන් රැගෙන යා හැකි ධාරිතාව අනුව ගණනය කෙරේ :.කේබලයේ හරස්කඩ ප්රදේශය ඉතා කුඩා නම්, කේබල් දිග ඉතා දිගු වේ, හෝ රේඛීය වෝල්ටීයතා පහත වැටීම ඉතා විශාල නම්, සම්ප්රේෂණ ධාරාව නිෂ්පාදනය සඳහා අවශ්ය වත්මන් අගයට ළඟා නොවේ. 1.6m ට වැඩි ටැංකි පළලක් සහිත ප්ලේටින් ටැංකිය සඳහා, ද්විපාර්ශ්වික බලය පෝෂණය කිරීමේ ක්රමය සලකා බැලිය යුතු අතර, ද්විපාර්ශ්වික කේබල්වල දිග සමාන විය යුතුය.මේ ආකාරයෙන්, ද්විපාර්ශ්වික වත්මන් දෝෂය යම් පරාසයක් තුළ පාලනය කිරීමට සහතික විය හැක.ප්ලේටින් ටැංකියේ එක් එක් පියාසර තීරුවේ දෙපැත්තටම සෘජුකාරකයක් සම්බන්ධ කළ යුතුය, එවිට කැබැල්ලේ දෙපැත්තේ ධාරාව වෙන වෙනම සකස් කළ හැකිය. (6) තරංග ආකෘතිය.වර්තමානයේ, තරංග ආකෘතියේ දෘෂ්ටි කෝණයෙන්, විද්යුත් ආලේපන සහ පිරවුම් වර්ග දෙකක් තිබේ: ස්පන්දන විද්යුත් ආලේපනය සහ DC විද්යුත් ආලේපනය.මෙම විද්යුත් ආලේපනය සහ සිදුරු පිරවීම යන ක්රම දෙක අධ්යයනය කර ඇත.සාම්ප්රදායික සෘජුකාරකය DC විද්යුත් ආලේපනය සහ සිදුරු පිරවීම සඳහා භාවිතා කරයි, එය ක්රියාත්මක කිරීමට පහසුය, නමුත් තහඩුව ඝන නම්, කළ හැකි කිසිවක් නොමැත.PPR සෘජුකාරකය ස්පන්දන විද්යුත් ආලේපනය සහ සිදුරු පිරවීම සඳහා භාවිතා කරයි, එහි බොහෝ ක්රියාකාරී පියවර ඇත, නමුත් ක්රියාවලියේ ඝනකම පුවරු සඳහා ශක්තිමත් සැකසුම් හැකියාව ඇත.
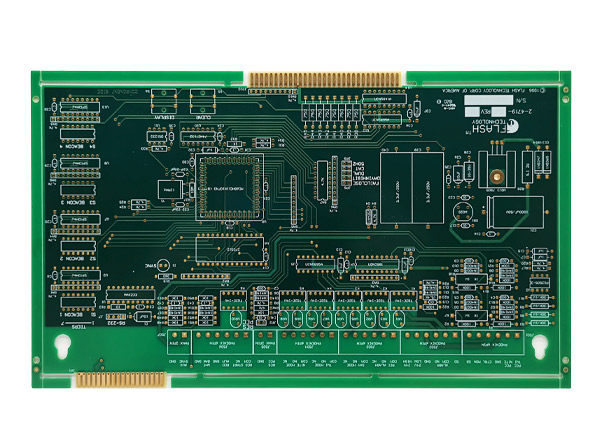
උපස්ථරයේ බලපෑම විද්යුත් ආලේපනය සහ සිදුරු පිරවීම සඳහා උපස්ථරයේ බලපෑම නොසලකා හැරිය නොහැකිය.සාමාන්යයෙන්, පාර විද්යුත් ස්ථර ද්රව්ය, සිදුරු හැඩය, දර්ශන අනුපාතය සහ රසායනික තඹ ආලේපනය වැනි සාධක ඇත. (1) පාර විද්යුත් ස්ථර ද්රව්ය.පාර විද්යුත් ස්ථරයේ ද්රව්යය සිදුරු පිරවීම සඳහා බලපෑමක් ඇත.වීදුරු තන්තු ශක්තිමත් කිරීම් වලට වඩා වීදුරු නොවන ශක්තිමත් කිරීම් සිදුරු පිරවීම පහසුය.කුහරය තුළ ඇති වීදුරු කෙඳි නෙරා යාම රසායනික තඹ වලට අහිතකර බලපෑමක් ඇති බව සඳහන් කිරීම වටී.මෙම අවස්ථාවෙහිදී, සිදුරු පිරවීමේ දුෂ්කරතාවය වන්නේ සිදුරු පිරවීමේ ක්රියාවලියට වඩා විද්යුත් රහිත තහඩු බීජ ස්ථරයේ ඇලවීම වැඩි දියුණු කිරීමයි. ඇත්ත වශයෙන්ම, සැබෑ නිෂ්පාදනයේදී වීදුරු තන්තු ශක්තිමත් කරන ලද උපස්ථරවල විද්යුත් ආලේපනය සහ සිදුරු පිරවීම සිදු කර ඇත. (2) දර්ශන අනුපාතය.වර්තමානයේ, විවිධ හැඩයන් සහ ප්රමාණවලින් සිදුරු සඳහා සිදුරු පිරවීමේ තාක්ෂණය නිෂ්පාදකයින් සහ සංවර්ධකයින් විසින් බෙහෙවින් අගය කරනු ලැබේ.සිදුරු පිරවීමේ හැකියාව සිදුරු ඝණකම හා විෂ්කම්භය අනුපාතයට බෙහෙවින් බලපායි.සාපේක්ෂ වශයෙන්, DC පද්ධති වඩාත් වාණිජමය වශයෙන් භාවිතා වේ.නිෂ්පාදනයේ දී, සිදුරේ ප්රමාණයේ පරාසය පටු වනු ඇත, සාමාන්යයෙන් විෂ්කම්භය 80pm~120Bm, සිදුරු ගැඹුර 40Bm~8OBm, සහ ඝනකම-විෂ්කම්භය අනුපාතය 1:1 නොඉක්මවයි. (3) විද්යුත් රහිත තඹ ආලේපන තට්ටුව.විද්යුත් රහිත තඹ ආලේපන තට්ටුවේ ඝනකම සහ ඒකාකාරී බව සහ විද්යුත් රහිත තඹ තහඩු දැමීමෙන් පසු ස්ථාවර කාලය සිදුරු පිරවීමේ ක්රියාකාරිත්වයට බලපායි.විද්යුත් රහිත තඹ ඉතා තුනී හෝ අසමාන ඝනකමක් ඇති අතර එහි සිදුරු පිරවීමේ බලපෑම දුර්වලයි.සාමාන්යයෙන්, රසායනික තඹවල ඝනකම පස්වරු 0.3ට වැඩි වූ විට සිදුරු පිරවීම නිර්දේශ කෙරේ.මීට අමතරව, රසායනික තඹ ඔක්සිකරණය ද සිදුරු පිරවීමේ බලපෑම මත ඍණාත්මක බලපෑමක් ඇත.